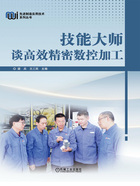
第一章 高效精密数控加工概述
一、高效精密数控加工技术
精密加工技术(High Precision Machining Technology)是获得高尺寸精度和表面完整性的必要手段。加工的精细化程度代表着一个国家制造业的发展水平。为适应产品小型化、轻量化、智能化和高集成化的发展趋势,数控加工技术不断向着精密和超精密方向开发及应用。
数控技术,即采用数字控制方法对某一工作过程实现自动控制的技术,在产品加工中扮演着越来越重要的角色,在大幅地提高产品加工质量和效率的同时,也大幅地降低了操作人员的劳动强度,在保障产品研制与批量生产中发挥了重要作用,因此数控技术是具有高效率与高精度的加工技术。
高效精密数控加工技术(Efficient Precision CNC Machining Technology)是以精密加工为核心,融入数控技术的现代制造技术,是制造业尖端领域的重要支撑技术,是现代高科技产业和科学技术的发展基础,也是现代制造科学的发展方向。高效精密数控加工技术是先进实用的制造技术,广泛应用于航空、航天、兵器及船舶等制造业,尤其在飞机制造业、船舶制造业更加受到重视,可大幅地提高生产效率,切削效率为传统切削效率的5倍以上,加工精度可达到0.001mm。实践证明,高效精密数控加工技术可大大缩短产品生产周期,加速新产品的开发。因此,高效精密数控加工技术具有强大的生命力和应用前景,是切削加工发展的主流。我国高效精密数控加工技术的开发与应用还处于初步阶段,每年进口大量高端数控设备,同时也研发多种高速、高效加工设备,只要我们充分认识高效精密数控加工技术的优越性和产生巨大经济效益的潜力,发挥我们自身数控加工技术优势,就一定会把我国的高效精密数控加工技术推进到一个新高度。
(一)精密加工技术的发展
精密加工技术的发展总共经历了三个阶段。
1)出于国家国防科技及航天技术的需求,美国开发了单点金刚石切削(Single Point Diamond Turning, SPDT)技术,也称为“微英寸技术”。1966年,美国联合碳化物公司(Union Carbide)、美国劳伦斯利弗莫尔实验室(Lawrence Livermore Laboratories)以及荷兰飞利浦公司(Philips)相继各自研发出超精密金刚石车床。1974年,Taniguchi使用纳米技术一词描述超精密机械加工。1983年,Taniguchi又对各时期的机械加工精度进行了总结并对其发展趋势进行了预测,在此基础上,Byrne等人描绘了20世纪40年代后加工精度的发展,如图1-1所示。纵观加工精度的发展历史可以看出,21世纪的精密加工水平已达到20世纪50年代的超精密加工水平。从机械加工行业发展的角度来讲,精密及超精密加工的界限是一个相对量,加工精度仅从尺度来描述是不够的,还应结合不同时代的科学技术水平,进行尺度、技术等多方面的综合描述。

图1-1 20世纪40年代后加工精度的发展
2)20世纪80~90年代为民用初期。美国政府于20世纪80年代,推动穆尔特殊工具公司(Moore Special Tool)等民间企业研制精密加工设备,日本东芝(Toshiba)、日立(Hitachi)以及欧洲的克兰菲尔德大学(Cranfield University)也陆续推出其精密加工设备,这些设备开始应用于一般民间工业光学组件商品的制造。但此时的精密加工设备依然高贵而稀少,主要以专用机的形式订做。20世纪80年代后期,美国对超精密金刚石切削机床的开发研究,投入了巨额资金和大量人力,实现了大型零件的微英寸精密加工。
3)20世纪90年代至今为民间工业应用成熟期。从1990年起,由于汽车、能源、医疗器材、信息、光电和通信等产业的蓬勃发展,所以精密加工设备的需求急剧增加,在工业界的应用包括非球面光学镜片、菲涅尔透镜、精密及超精密模具、磁盘驱动器磁头、磁盘基板加工以及半导体晶片切割等。在这一时期,精密加工设备的相关技术,例如控制器、激光干涉仪、空气轴承精密主轴、空气轴承导轨、油压轴承导轨和摩擦驱动进给轴等的研制技术也逐渐成熟,精密加工设备成为工业界常见的生产机器设备,许多公司、甚至是小公司也纷纷推出量产型设备。此外,设备精度也逐渐接近纳米级水平,加工行程变得更大,加工应用也逐渐广泛,除了金刚石车床和超精密研磨外,超精密五轴铣削和飞切技术也被开发出来,并且可以加工非轴对称、非球面的光学镜片。
目前,世界上的精密加工强国以欧美国家和日本为先,但两者的研究重点并不一样。欧美国家出于对能源或空间开发的重视,比如美国,几十年来不断投入巨额经费,对大型紫外线、X射线探测望远镜的大口径反射镜的加工进行研究。日本对超精密加工技术的研究相对美国、英国来讲起步较晚,却是当今世界上超精密加工技术发展较快的国家。日本超精密加工的应用对象大部分是民用产品,包括办公自动化设备、视像设备、精密测量仪器、医疗器械和人造器官等。日本在声、光、图像、办公设备中的小型、超小型电子和光学零件的超精密加工技术方面,具有优势,甚至超过了美国。日本超精密加工最初从铝、铜轮毂的金刚石切削开始,而后集中于计算机硬盘磁片的大批量生产,随后是用于激光打印机等设备的多面镜的快速切削。随着科技的不断发展,精密加工技术不断发展更新,加工精度不断提高。虽然不同国家对于精密加工技术的研究侧重点不同,但推动其发展的主要因素是相同的:对产品高质量的追求、对产品小型化的追求及对产品性能的追求。
(二)高效精密数控加工的影响因素
制造过程是指将能量流、物质流、信息流通过机械加工转化为产品的过程,即把原材料、毛坯转化为成品的过程,包括毛坯制造、机械加工、检验等过程,如图1-2所示。因此,加工效率及成品的精度受到如下几个因素的影响。

图1-2 制造过程示意
1.毛坯制备
毛坯质量是保证最终成品质量的基础。毛坯的形状和尺寸取决于成品的形状和尺寸。毛坯是在成品需要加工的表面上,增加一定的机械加工余量。毛坯制造时,同样会产生误差,毛坯制造的尺寸公差称为毛坯公差。毛坯加工余量和公差的大小,直接影响机械加工的劳动量和原材料的消耗,从而影响产品的制造成本。因此,现代机械制造的发展趋势之一,便是通过毛坯精化,使毛坯的形状和尺寸尽量与零件一致,需要配合的部位与尺寸精度要求高的部位预留加工余量,力求作到少、无切削加工。
2.加工机理
根据加工方法的机理和特点的不同,精密加工方法可以分为:去除加工、结合加工和变形加工三大类,见表1-1。
表1-1 精密加工方法分类

根据加工方法的机理、特点以及传统状况来看,精密加工又可分为非传统加工、传统加工以及复合加工。非传统加工是指利用电能、磁能、声能、光能、化学能和核能等对材料进行加工和处理;传统加工是指刀具切削加工、固结磨料和游离磨料的磨削加工;复合加工是采用多种加工方法的复合作用,进行优势互补,相辅相成。目前,在实际运用中,占主要地位的仍是传统加工方法。
近年来,在非传统加工中,出现了电子束、离子束、激光束等高能加工、微波加工、超声加工、蚀刻、电火花和电化学加工等多种方法,特别是复合加工,如磁性研磨、磁流体抛光、电解研磨及超声珩磨等,在加工机理上均有所创新。在加工机理上特别提出了以快速成形为代表的“堆积”加工,这在加工技术上具有里程碑意义。在传统加工方法中,占主要地位的加工方法有:金刚石刀具超精密切削、精密高速切削、金刚石微粉砂轮超精密磨削和精密砂带磨削等。
3.加工设备——机床精度、刀具角度
机床作为机械制造业的基础装备,在为刀具和工件装夹提供基础支撑的同时,还为所需要加工要素的形成提供各种相应的运动。机床的精度包括几何精度和传动链精度。机床的传动链误差对一般圆柱面、平面的加工精度没有影响,但会对工件与刀具具有严格内联系的加工表面的精度产生影响。例如,在车削螺纹时,机床的传动链误差是影响精度的主要因素。机床的几何精度对加工精度的影响较大,主要体现在机床主轴的回转精度和机床导轨的直线运动精度。因为机床一般是通过主轴将动力传递给工件或刀具,所以主轴的回转精度对加工精度有直接的影响,其主要表现形式为轴向窜动和径向圆跳动。因此,机床自身精度的高低对加工精度有着决定性的影响。
合理的刀具使用,可以提高工件的表面质量。以金属切削过程为例:金属切削过程是指刀具与工件运动并相互作用的过程,其机理是刀具切削刃和前刀面对工件的推挤、摩擦,使切削层金属发生剪切滑移变形和摩擦塑性变形而形成切屑。后刀面与工件挤压形成加工表面,切削过程如图1-3所示。

图1-3 金属切削过程
刀具角度可以控制切屑的类型(见图1-4)和流向,减少切屑与工件已加工表面的接触,进而提高工件的表面精度。在加工不同刚度的工件时,改变刀具的主偏角大小,能明显减小加工过程中的机械振动和工件变形,从而降低已加工表面的表面粗糙度值。

图1-4 切屑类型
4.加工环境与工艺规程
精密机械加工对作业环境的要求很严格。一般来说,在产品设计阶段假设车间环境是相对稳定的,但在实际加工过程中,环境温度、湿度和机床的清洁度都会发生变化。对于磨削类型的加工,工件表面在环境的影响下可能造成暂时性的光滑,从而导致表面粗糙度、光滑度无法满足设计要求。此外,精密加工现场的抗振性、防电磁干扰、清洁度等因素都会影响到产品质量。因此,精密加工需要在专业的精密加工车间内进行。
工艺规程是以文件形式规定的工艺过程,其形式包括工艺过程路线表、工序卡、工序检验卡及机床调整卡。合理的工艺规程可为加工提供科学的指导,保障产品的质量。
5.高速切削
高速切削加工技术(High Speed Machining Technology)的概念是由德国Carl. J. Salomon博士提出的。他认为每一种材料在加工时都存在一个临界切削速度,当切削速度小于材料的临界切削速度时,切削温度将随着切削速度的增加而提高,同时刀具磨损也将持续增大,这对工件加工表面的质量和刀具寿命将产生不利影响。但随着切削速度的增加,当切削速度大于材料的临界速度后,温度、刀具磨损以及切削力都会下降,从而提高工件的表面质量,刀具寿命、生产效率也可以得到极大的提升,如图1-5所示。

图1-5 萨洛蒙曲线
目前,在金属切削研究中,高速切削还没有统一的概念,通常使用切削速度进行定义,高速切削进给速度为常规切削的5~10倍。高速切削分高速铣削、高速车削及高速钻孔等,高速切削针对薄壁件非常适合,可提高表面精度,同时省去后续的精磨工序。高速切削是相对的,不同的材料具有不同的切削速度范围,因而其高速切削速度的范围也不尽相同。例如,目前加工铝合金切削速度已达到2000~7500m/min,钢为600~3000m/min,超耐热镍基合金为80~500m/min。高速切削作为一种重要的先进加工技术,是国内外在加工领域中的重要研究对象,对我国的制造业发展具有非常重要的意义。
6.误差测量与补偿技术
数控机床是制造业的基础,高精度、高效率、高稳定性是机械加工制造领域永不停歇的追求目标。航空、航天、能源、微电子及生物医疗等领域高精尖复杂产品的加工生产,向现代制造工艺、装备和系统的极限性能不断提出新的挑战。数控机床作为现代制造业的“工业母机”,其精度要求受到各国专家、学者的关注。近年来,如何对影响加工精度的机床误差进行测量、补偿,已成为研究热点。
现代制造业中,普遍将误差元素分为三大类。
(1)加工前固有的因素引起的误差 包括:①原理(理论)误差;②机床夹具和刀具的制造误差,机床、夹具在加工过程中的磨损。
(2)加工中产生的因素引起的误差 包括:①机床调整(对刀)误差;②装夹误差;③加工过程中的切削力;④加工过程中的切削热;⑤刀具磨损;⑥毛坯残余应力;⑦切削参数。
(3)加工后出现的因素引起的误差 包括:①残余应力变形;②测量误差。
在加工过程中,各类误差元素作用于成形过程,使刀具与工件的实际相对位置偏离理论值,形成加工误差。在所有误差元素当中,机床、夹具和刀具的制造误差和加工过程中的热引起的误差总共占了所有误差的45%~65%。
误差补偿技术(Error Compensation Technique)是一种改善机床加工精度的“软”技术,即针对机床存在的误差元素建立精确的数学模型,通过软件手段来人为制造出与实际误差大小相同、方向相反的误差,叠加到机床的实际运动过程中,从而实现对原有误差的补偿。
为了提升我国基础装备制造业的技术水平,缩小与国外高档数控机床的技术差距,我国于2009年开展了“高档数控机床与基础制造装备”的国家重大专项研究工作,其中,误差测量与补偿技术的研究是重点方向之一。
(三)发展高效精密数控加工的意义
精密数控加工技术是推动机械制造业深化发展的源动力,是工业4.0时代的核心动能,未来精密机械加工技术将朝着高精度、智能化的方向持续发展。因此,大力发展高效精密数控加工技术,具有以下重要意义。
1)高效加工可提高单位时间内材料去除率,减少切削加工时间,提高加工效率,降低制造成本。
2)高效加工切削速度大,切屑高速排出,可带走90%以上切削热。由于工件的切削热大量减少,因此有利于减少工件的热应力,提高工件的加工精度。
3)高效加工切削速度大,切削力随之减少,大致平均减少35%以上,有利于减少工件切削应力,对弱刚度薄壁结构件,有利于提高其加工精度。
4)高效加工可加工高硬度淬火金属材料,替代电加工和磨削加工,缩短产品研发与批量生产制造周期,降低加工成本。