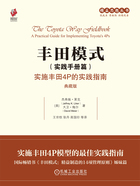
内部和外部的目的感
何为组织的目的感呢?如果仅仅是为了赚钱,那么在一张海报上画一个大大的美元标志给员工和管理人员看就可以了,根本无须费心去准备使命宣言。如果公司的目的不止于此,那么你应该考虑一下:公司在内部和外部打算实现什么目标?公司打算为内部利益相关者创建什么?想让他们奉献什么?而他们又能获得什么回报?公司对外界有何影响?此外,公司的使命应当包含两个部分——一部分关于员工,另一部分关于公司。
图2-1展示的是公司目的,它将员工和与公司相应的内部和外部目标结合起来,构成了一个矩阵。图中包含了对丰田公司目标的简要陈述,并分别指明了公司的短期目标和长期目标。

图2-1 明确公司目的
对于矩阵中每一单元格的短期目标,每一家公司都渴望实现:有能力的内部流程、有能力的员工、尽职尽责的合作伙伴以及能够赚到钱。这些都非常简单易懂,比较难的部分是如何让公司高层真正地思考公司的长期目标。下面,让我们了解一下每个单元格中的长期目标是什么含义。
精益体系
为简明起见,我们首先从丰田最为世人所熟知的部分谈起——丰田生产方式的技术部分。通过消除不能创造价值的浪费,丰田生产方式缩减了从客户下单至交货的时间,其结果是创建了一个能够以低成本、即时将高品质产品交付给客户的精益流程,并且使得丰田可以在无须维持大量库存的情况下盈利。在产品开发领域,你同样可以发现相似的精益流程。丰田不仅拥有业界最快的开发速度,而且在为客户更新车型和特性的速度、产品品质及成本方面均要优于其竞争对手。如今,精益内部流程已扩展至丰田的各个业务支持职能部门,其中包括销售、采购、生产、企划等,只不过这些领域的精益流程不像制造和产品开发领域的精益流程那么正式罢了。
精益体系并非仅限于工具和技术,其实理念也是很重要的一部分,很多人对这一点还缺乏足够的认识。比如,“如何使用精益体系杜绝浪费,从而带来即时的财务收益”,对此人们很容易理解,但是,“为了杜绝长期的浪费而有必要创造短期的浪费”这一点又如何理解呢?考虑以下场景:
1.将能创造价值的工人当作外科医生来看待,并在不打扰他创造价值的工作的情况下为其准备好工作所需的所有工具和零部件,这可能需要一些非创造价值的准备工作。工具和零部件可能需要提前准备好并放置到一个大小适中的容器或工具箱中,而货物搬运人员则需要将这些常用物品搬运到进行工作的场所。
2.为了减少批量和改进零部件在整个系统内的运输流程,可能需要频繁更换某个设备工具,从而产生额外的装配费用。快速换模(SMED)程序可以极大地降低装配时间和费用,但许多公司却将节省下来的时间用来生产更多的零部件。因此,这不仅没有减少批量,反而加剧了生产过剩的程度。
3.为了改善质量、缩短产品开发流程的提前期,可能需要配备专门的总工程师。总工程师只需负责项目的运行,而无须管理项目参与人员。这是在普通项目管理人员之外,额外增加的一个职位。总工程师责任重大,应为之提供高薪。
4.为改善产品的质量,可能需要在产品研发流程的初期就让供应商参与进来,并应选择与技术过硬的供应商合作,这样可能会导致产品初期成本增加,无法成为最低成本产品的生产商。
换言之,为了建立高质量精益流程,实现长期成本节省,有必要进行短期投资。况且我们可能很难精确计算出对于某一特定行为所进行的投资到底能节省多少资金。比如,与频繁更换工具的成本相比,减少批量所带来的收益是多少呢?劳动力成本比较容易计算,但是较小批量的收益却难以把握。实际上,如果我们能够逐一计算每项改进活动所带来的收益,也就不用谈论什么精益体系了。因此,尽管表面上看,精益体系只是简单的技术问题,但本质上而言,它更是一个理念。
误区 将精益体系视为零碎的技术项目
精益工具的功能非常强大。比如,许多公司都开办了为期一周的经营改善工作坊,并发现这些精益工具可以一举多得,如节省空间、提高生产力、提高质量等——这东西真不错!甚至有些公司在每次工作坊结束时都会计算一下自己的投资收益。但是,真正的精益体系要求具有一个连贯的价值流,而这绝非是个别的改善工作坊(kaizen workshop)所能实现的。况且,有些投资的回报更加难以把握。不要通过验证每个零碎的改进成效来发展精益体系,尽管通过这种方法你可能获得一些唾手可得的成果,但它无法帮助你建立起一个持续消除浪费的体系,从而使你失去了实现长期更大盈利的机会。
学习型社会群体
在丰田的许多部门,TPS是指“思维生产体系”(thinking production system)。当大野耐一连接各种流程,以消除各个步骤之间的浪费时,他获得了一个惊人的发现。当各个流程连接在一起之后,各种问题立即变得显而易见,人们不得不思考解决之法,否则就会导致流程中断。这个发现一经获得,便不再是偶然现象。大野耐一发现,精益体系的真正强大之处在于,它可以使问题浮现,并迫使人们思考以寻求解决之法。
然而,如果不将个人所学到的东西与他人分享,那么这种效力对公司的影响极其有限。重新发现问题并找出解决之法本身就是一种浪费。因此,为了汲取实施各种对策时获得的知识,我们必须对学习系统进行投资,使这种知识可以再次应用。而学习又可以为今后的深入学习树立新的标准、创建新的学习高原。
创建学习型社会群体的含义是,某个社会群体中拥有多个具备学习能力的人员,这是基本条件。此外,社会群体表明了一种归属关系,因此,创建社会群体需要让其成员具有归属感。一旦经济形势恶化便会被随时解雇的临时工将不属于该群体。归属某一社会群体还意味着互惠:成员为社会群体做贡献,而社会群体对其成员同样要有所回报。
实际上,丰田对其员工进行了巨大的投资,本书第11章将对此进行深入讨论。比如,要培养一位能够完成丰田所期待的基础工作的一流工程师大约需要经历一个为期3年的投资期。因此,如果一名工程师不到3年便离开了丰田,那么这笔投资就彻底失败了。之所以要进行为期3年的投资,是因为丰田要教会员工如何按照丰田模式思考、解决问题,进行有效交流以及实施工程任务,这可不像学习基本技术技能那样简单。
据我们观察,丰田依据丰田模式的长期理念来看待员工。若不是有这种长期理念支持,丰田也不会对员工做出长期投资。这一理念为员工提供了一个框架,员工可以在此框架内实施个人行动。
精益企业
丰田的理念一直处于不断更新与完善之中。由于丰田汽车70%~80%的零部件都是由外部供应商设计和创建的,因此,只有拥有一流的供应商,才能有优质的丰田产品。丰田认识到,一旦产品中出现不合格零部件,客户不会因为零部件是由外部供应商提供的而原谅丰田,丰田需要对这些零部件负责任。负责任的唯一方式就是确保供应商和丰田拥有同等水平的精益体系,将它们培养为学习型社会群体和精益企业。这些供应商是价值流的一部分,同时也是精益体系的一部分。
因此,丰田经常对合作伙伴进行投资,这看起来似乎有违常理。但是,不要忘记多年前发生的一个实例。当时,丰田的供应商p阀工厂因大火而被烧毁。p阀是全世界所有丰田汽车刹车系统中一个至关重要的组件,而当时丰田犯了一个大错:只让一家供应商的一家工厂生产这种阀门。大火之后,整个供应链中的p阀供应最多维持3天,面对这种情况,总计200家供应商和子公司不得不在供应断掉之前,自行组织起p阀的生产和运营。其中有63家不同的公司在丰田未提出要求的情况下,便自发地使用它们自己的设备开始生产p阀。这样的忠诚度价值多少?它使得丰田可以充满自信地经营一条精益供应链,即使遇到危机,丰田也可以调动大量的资源来解决问题。这一生动的案例证明,丰田通过大力投资精益企业,为自己创造了一个强大的战略武器。
创造价值贡献者
丰田管理者每天很早就去上班,制定正确的长期决策,他们的驱动力是什么?如果他们的目标像一些经济理论所说的那样,只是为使员工发挥最大的效用,他们就不会那么做了。丰田汽车销售公司的执行副总裁兼首席执行官吉姆·普莱斯(Jim Press)曾经坦承他的总收入要比美国汽车公司同等职位人员的收入少很多。当被问及为什么能够忍受这种收入差距时,他回答说:“我的收入不错,我很满足。能在这里工作我深感荣幸。公司赚钱是为了在将来能够再投资,为了我们能够继续生存……以造福社会、造福社区。”
这些话如果出自他人之口,我们可能会报以不置可否的微笑,但心里会想:这是多么天真可爱但完全不实际的想法啊。但是吉姆·普莱斯是认真的,他真的这么认为。而且作为丰田在北美地区的高级主管之一,凭借这个信念,他可以影响非常多的人。
如果返还股东红利和支付高层丰厚的奖金是唯一目的,丰田就不会付出这么大的努力来变成一家精益企业了,也没有必要投资创建一个学习型社会群体。就连精益体系也只是需要刀耕火种这种原始的精益手段来帮助降低短期的成本就足够了。因此,与一切相关的是理念,如果没有这些基本的理念,丰田的4P金字塔模型就会坍塌。
小建议 成功的诀窍
开发一套精益体系与为退休攒钱的做法相似。为了将来能够获得收益,短期内必须付出艰苦的努力和牺牲。执行流程将需要牺牲时间和资源,以获取未来潜在的收益。和投资一样,成功的诀窍在于尽早开始,并定期投入。