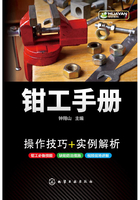
第4章 錾削
4.1 錾削基本技能
用手锤打击錾子对金属工件进行切削加工的操作称为錾削。錾削加工主要进行工件表面的粗加工、去除铸造件的毛刺和凸台、分割材料和錾削油槽。
4.1.1 錾削工具
錾削的主要工具是錾子和手锤。
(1)錾子
錾子的种类很多,钳工常用錾子的种类主要有扁錾(平錾)、尖錾(窄錾)和油槽錾三种,如图4-1所示。扁錾主要用来錾削凸缘、毛边和分割板料,应用最为广泛;尖錾主要用来錾削槽和分割曲线形板料;油槽錾主要用来錾削油槽。

图4-1 錾子的种类
錾子是錾削工件的刃具,一般用碳素工具钢(T7A、T8A)经锻打成形、刃磨和热处理制成,其硬度不小于62HRC。
1)錾子结构
图4-2所示为扁錾的结构。錾子的结构主要由錾刃(切削部)、錾身和錾头三部分构成。錾刃是由前、后刀面的交线形成;錾身的截面形状主要有八角形、六角形、圆形和椭圆形,使用最多的是八角形,便于掌控錾子的方向;錾头有一定的锥度,錾头端部略呈球面,便于稳定锤击。

图4-2 扁錾的结构
2)錾子的几何形状及角度
图4-3给出了扁錾、尖錾的几何形状及角度。

图4-3 錾子的几何形状及角度
① 楔角(β)。由前、后刀面形成的夹角称为楔角。楔角越大,切削部的强度越高,但切削时的阻力也就越大。錾子楔角的大小,要根据加工材料的软硬性质来确定,具体参数可参照表4-1选取。
② 斜面夹角(ε)。由上斜面和下斜面形成的夹角称为斜面夹角,具体参数如表4-1所示。
③ 副偏角(κτ)。由腮面与錾身轴线形成的夹角称为副偏角,具体参数如表4-1所示。
④ 錾头锥角(γ)。錾头锥体的夹角称为錾头锥角,具体参数如表4-1所示。
表4-1 錾子技术参数

⑤ 錾刃宽度(B)。由左、右腮面形成的刃线长度称为錾刃宽度,具体参数如表4-1所示。
⑥ 切削部长度(l)。自錾刃至錾肩且平行于錾身轴线的长度称为切削部长度,具体参数如表4-1所示。
⑦ 錾身长度(L)。自錾刃至錾头球面的长度称为錾身长度,具体参数如表4-1所示。
⑧ 錾身宽度(b)。錾身平行面之间的距离称为錾身宽度,具体参数如表4-1所示。
(2)手锤
手锤是由锤头、锤柄和楔铁构成的,如图4-4所示,是钳工常用的锤击工具。

图4-4 手锤结构
其中,锤头由T7、T8碳素工具钢制成,两端锤击部位经过热处理,其硬度不小于62HRC。锤头的规格以其重量来表示,钳工常用的有0.45kg(lb)、0.68kg (1.5b)和0.91kg(2b)三种。楔铁的形状为楔形,厚度为5mm左右,由斜面、倒刺和楔尖构成,锤柄装入锤孔后要用楔铁楔紧,以防锤头脱离。锤柄一般选用比较坚韧的木材制成,如檀木等。常用锤柄的长度为350mm左右。
4.1.2 錾削工具的使用及錾削姿势
錾削加工是手工操作,其加工质量与其操作手法应用的正确性关系极大,因此,錾削操作首先应掌握錾削工具的正确使用以及正确的錾削操作姿势。
(1)錾子的握法
錾子主要用左手的中指、无名指和小指握住,食指和大拇指自然地接触,常用的握法有两种。
① 正握法。手心向下,腕部伸直,用中指、无名指握住錾身,食指和大拇指自然伸直,小拇指自然收拢即可,錾头露出虎口10~15mm,如图4-5(a)所示。

图4-5 錾子的握法
② 反握法。手心向上,大拇指与食指、中指、无名指相对捏住錾身,手掌悬空,如图4-5(b)所示。
(2)手锤的握法
手锤用右手握住,采用五个手指满握的方法,大拇指轻轻压在食指上,虎口对准手锤方向,锤柄尾端露出约15~30mm。
手锤在敲击过程中,手指的握法有两种。一种是五个手指的握法,无论是在抬起锤子或进行捶击时都保持不变,这种握法叫紧握法。紧握法的特点是在挥锤和落锤的过程中,五指始终紧握锤柄,如图4-6(a)所示。另一种握法是在抬起锤子时,小指、无名指和中指依次放松;在落锤时,又以相反的顺序依次收拢紧握锤柄。松握法的特点是手不易疲劳,锤击力大,如图4-6(b)所示。

图4-6 手锤握法
(3)挥锤的方法
挥锤方法分为腕挥法、肘挥法和臂挥法三种。
① 腕挥法。腕挥法是以腕关节动作为主,肘关节、肩关节相协调进行的一种挥锤方法,如图4-7所示。

图4-7 腕挥姿态
腕挥法的特点是腕关节的动作幅度为40°(110°-70°=40°)左右,前臂的挥起幅度为40°(10°+30°=40°)左右,手锤的挥起幅度为80°(140°-60°=80°)左右。由于手锤的挥起幅度较小,因而锤击力量也比较小,一般用于起錾、收錾和精錾,腕挥时采用紧握法握锤。
② 肘挥法。肘挥法是以肘关节动作为主,肩关节、腕关节相协调进行的一种挥锤方法,如图4-8所示。

图4-8 肘挥姿态
肘挥的动作特点是前臂与水平面大致成80°,前臂的挥起幅度为90°(80°+10°=90°)左右,手锤的挥起幅度为140°(200°-60°=140°)左右。由于手锤的挥起幅度较大,因而锤击力量也比较大,肘挥时采用松握法握锤。
③ 臂挥法。臂挥法是以肩关节动作为主,前、后臂大幅度动作的一种挥锤方法,如图4-9所示。

图4-9 臂挥姿态
臂挥的动作特点是后臂提起与铅垂面大致成90°,前臂的挥起幅度为110°(100°+10°=110°)左右,手锤的挥起幅度为150°(210°-60°=150°)左右。由于挥锤位置为最高极限,因而手锤的挥起幅度最大,所以锤击力量也最大,一般用于大力錾削,臂挥时采用松握法握锤。
(4)錾削的姿势
錾削时,操作者站在钳台前,站位如图4-10所示。左脚与台虎钳中心线成30°,右脚与台虎钳中心线成75°。
要保证站立挥锤时落点对准錾子的端部,握錾子手的小臂应保持水平位置,肘部不能下垂,也不能抬高,以免影响錾子的切削角度,如图4-11所示。

4.1.3 錾削基本操作技术
錾削是用手锤锤击錾子,以对金属进行切削加工的操作,主要用于不便于机械加工的场合,或在余量太多的部位去掉足够的余量。錾削的基本操作主要有以下几方面的内容。
(1)錾削工艺参数的确定
图4-12给出了錾子錾削的操作简图。

图4-12 錾削的操作
其中,錾身中心线与已加工表面间的夹角θ称为錾身倾角,如图4-12(a)所示。錾身倾角的大小应根据錾刃楔角的大小来确定,具体角度值如表4-2所示。
表4-2 錾削技术参数

后刀面与已加工表面间的夹角α称为錾身后角,如图4-12(a)所示。若后角过大,錾刃容易向下錾;若后角过小,錾刃容易向上滑出加工表面。因此,后角的角度值很小并在加工中要始终稳定在5°~8°。
已加工表面与待加工表面间的垂直距离ap称为錾削量,如图4-12(a)所示。錾削量受工件材质、加工余量、质量要求和个人力量等因素的制约。若过深,则阻力太大,甚至錾不动;过浅,则效率较低。所以,錾削量一般控制在0.5~2.5mm。加工中应注意粗錾及錾削软材料时,可适当深一些;精錾和錾削硬材料时,可适当浅一些。
切削刃切入过渡表面的长度aω称为錾削宽度,如图4-12(b)所示。用扁錾进行加工时,一般是将切削刃长度的2/5~3/5的部分作为錾削宽度进行加工。这样,阻力就相对小些,效率也高些,加工质量也能得到保证。当过渡表面等于或大于切削刃长度时,则宜采用展成法进行錾削加工,如图4-12(c)所示。
已加工表面与钳口上平面间的垂直距离h为加工高度,如图4-12(d)所示。一般情况下,加工高度控制在1~3mm。被夹持工件的已加工表面离钳口愈高,则加工时的反弹和振动就愈大;反之,就愈小。这对錾削这种瞬间冲击的切削加工尤为重要。因此,应尽可能降低加工高度,从而最大限度地减少反弹和振动,以保证加工质量。
錾头球面高出握持手虎口上的垂直距离H为錾头露出高度,如图4-12(e)所示。一般情况下,錾头露出高度稍低一些,握持手对錾身的控制效果就会好一些;若过高,就会一定程度地影响錾身倾角的稳定性和锤击的准确性。因此,錾头高度一般控制在10~15mm。
(2)锤击速度
錾削时的锤击要稳、准、狠,要有节奏。挥锤到一定高度位置时,要有一个短暂的停顿,然后再用力落锤进行锤击。一般情况下,腕挥时约为40次/min,肘挥时约为35次/min,臂挥时约为30次/min。
(3)錾削操作注意事项
① 工件一般应夹持在台虎钳的中间位置,伸出高度离钳口10~15mm,工件下面要加木衬垫。
② 手柄与锤头若有松动时,应及时将楔铁楔紧;若发现手柄有损坏,应及时更换;手柄上不得沾有油脂,防止使用时手柄滑出而发生事故。
③ 錾子头部出现明显的裙边毛刺时,应该及时磨去。
④ 手锤的锤头应向前纵向放置在台虎钳的右边,柄尾不可露出钳桌边缘;錾子的錾刃应向前纵向放置在台虎钳的左边且不可露出钳桌边缘。
⑤ 锤击时,眼睛要始终看着錾子的刃尖部位,要随时观察錾削状况,而不要看着錾头部位,这样反而容易打手。
⑥ 进行臂挥操作时,应先挥2~4次的过渡锤,即由腕挥(1~2锤)过渡到肘挥(1~2锤),再由肘挥过渡到臂挥,同时力量也是由轻逐步过渡到重。
4.1.4 各个錾削阶段的操作
对于去除多余材料类的錾削加工(主要包含錾削平面、直槽、油槽等加工),其操作主要包括起錾、中途錾削、收錾等几个阶段,各个錾削阶段的操作方法主要有以下几方面的内容(对于板料的錾断类操作参见本章“4.2.5板料的錾削操作”的相关内容)。
(1)起錾
在工件的边缘先行錾出一个斜面作为錾刃定位面的操作称为起錾。起錾分为斜角起錾和正面起錾两种方法。
① 斜角起錾。在錾削平面时,先在工件的边缘棱角处,将錾身倾角置为-θ角(-30°左右),錾出一个斜面的方法称为斜角起錾,如图4-13(a)所示。起錾完成后再按照正常的錾身倾角进行中途錾削。
② 正面起錾。在錾削槽时,必须采用正面起錾,即在起錾时,錾刃全部贴住工件錾削部位的端面,将錾身倾角置成-θ角(-30°左右),錾出一个斜面,如图4-13(b)所示。起錾完成后再按照正常的錾身倾角进行中途錾削。

图4-13 起錾方法
(2)中途錾削
当起錾完成后,即进入中途錾削阶段。在此阶段,要注意三个问题:一是要注意錾身倾角的稳定,二是要注意錾刃与已加工表面的平行状态,三是要注意锤击要有节奏。
(3)收錾
每遍錾至尽头边缘并将要收尾时的錾削称为收錾。收錾分为调头收錾和直接收錾两种方法。
① 调头收錾。当錾削到离尽头边缘大约有10mm时,采取调头錾去剩余部分的方法称为调头收錾。当工件材料为铸铁和青铜时,必须采用调头收錾的方法錾去剩余部分,以防止工件边缘发生崩裂,如图4-14所示。

图4-14 錾到尽头时的方法
② 直接收錾。当錾削到离尽头边缘大约有10mm时,采取由臂挥过渡到肘挥,再由肘挥过渡到腕挥,通过逐步减轻锤击力量并直接錾削到尽头边缘的方法称为直接收錾。当工件材料为钢件或不便进行调头收錾时,可采用直接收錾。
4.1.5 錾子的热处理操作
錾子的热处理操作包括淬火和回火两个过程,其目的是保证錾子的切削部具有较高的硬度和一定的韧性。錾子的热处理通常安排在錾子粗磨后进行,即錾子按以下加工工艺进行刃磨及热处理:粗磨→淬火→回火→精磨。
(1)淬火
淬火是将工件加热到奥氏体后以适当方式冷却获得马氏体或贝氏体组织的热处理工艺。当錾子的材料为T7、T8碳素工具钢时,可把切削部约20mm长的一端放在炉膛内温度较高处,均匀加热至780~800℃(呈樱红色)后用圆钳或方钳夹住取出,并将錾子的淬火部位(长度4~6mm)垂直放入水中进行水淬,淬火部位在水中冷却时,应沿着水面缓慢移动。其目的是:加速冷却,提高淬火硬度;使淬火部位与不淬硬部分不致有明显的界线,以避免錾子在此线上产生裂纹。
(2)回火
回火是将工件淬硬后加热到Ac1以下的某一温度,保温一段时间,然后冷却到室温的热处理工艺。錾子的回火是利用其本身的余热进行的。当淬火部位露出水面的部分呈现黑色时,即由水中取出,迅速擦去氧化皮,观察淬火部位的颜色变化。颜色变化的基本顺序是白色→黄色→红色→蓝色→黑色,这个时间很短,只有几秒钟。在淬火部位介于红色和黑色之间,呈现蓝色时,将切削部放入水中进行冷却,俗称得“蓝火”;在淬火部位介于白色和红色之间,呈现黄色时,将切削部放入水中进行冷却,俗称得“黄火”。至此就完成了錾子的淬火和回火处理的全部过程。“黄火”的硬度比“蓝火”高些,不容易磨损,但脆性较大,容易崩刃,“蓝火”的硬度比较适中。当錾子的材料为T7、T8碳素工具钢时,扁錾一般采取得“蓝火”的回火处理,尖錾和油槽錾一般采取得“黄火”的回火
处理。
(3)錾子的热处理工艺及硬度
表4-3给出了不同钢号錾子的热处理工艺及硬度。
表4-3 不同钢号錾子的热处理工艺及硬度

4.1.6 錾子刃磨操作技术
在錾削操作过程中,免不了要对錾钝的錾子进行刃磨,錾子的刃磨操作方法主要有以下几方面。
(1)錾子刃磨时的握法
右手大拇指与其他四指左右相对捏住錾子的两腮面,以控制錾子刃磨时的左右移动,左手大拇指与其他四指上下相对捏住錾身尾部两平行面,以控制錾子刃磨时的楔角值,如图4-15(a)所示。

图4-15 錾子的刃磨
(2)刃磨方法
双手握錾在砂轮的轮缘面上进行刃磨,刃磨时,錾刃必须高于砂轮水平中心线,一般在砂轮水平中心线上30°~60°的范围内进行刃磨,如图4-15(b)所示。要在轮缘的全宽面上作左右移动,同时要控制好錾子的位置和角度,以保证刃磨出所需要的楔角值和平直的刃线(刃线要平行于斜面)。刃磨时施加在錾子上的压力不宜过大,左右移动要平稳,要及时蘸水冷却以防止退火。
(3)刃磨步骤
① 首先目测錾身的两组相互垂直的平行平面是否基本平行和垂直,必要时可刃磨处理。
② 磨平两斜面。先磨平一斜面,目测此斜面与錾身平面基本平行即可;再磨平另一斜面,目测此斜面与錾身平面基本平行即可,同时注意控制斜面夹角(ε)。
③ 磨平两腮面。先磨平一腮面,此腮面要基本垂直于一个选定斜面;再磨平另一腮面,此腮面也要基本垂直于选定斜面,同时注意控制刃口宽度(B)和副偏角(κτ)。
④ 粗磨前、后刀面。
⑤ 按照要求磨出錾头锥面。
⑥ 精磨前、后刀面。注意两个刃磨难点,一是要通过角度样板保证楔角值(β)在要求范围内,二是要目测刃线平直并且平行于选定斜面,即刃线要基本平行于刀面与斜面的交线。注意,精磨操作是在完成热处理后进行的。
⑦ 精磨两腮面。保证刃口宽度(B)的尺寸要求和副偏角(κτ)的角度要求。
(4)刃磨操作安全规程
① 砂轮外圆柱表面(工作面)必须平整。
② 开动砂轮机后必须先观察旋转方向是否正确,并要等到转速稳定后才可进行刃磨。
③ 刃磨时,操作者应站立在砂轮机的斜侧位置,不能正对砂轮的旋转方向。
④ 操作者一人进行刃磨时,不允许其他人员聚拢围观。
⑤ 刃磨时,必须戴好防护眼镜。
⑥ 禁止戴手套或用棉纱包裹刃磨錾子。
⑦ 刃磨时,不要用力过猛,以防打滑伤手。
⑧ 刃磨时,应及时蘸水、冷却,以防止刃尖部退火。
⑨ 刃磨结束后应随手关闭电源。