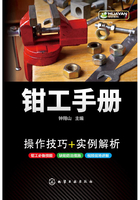
1.7 测量
在机械设备的装配、维修操作过程中,除需用计量器具对参与装配、维修的工件进行测量外,还需经常用计量器具对所装配、维修的零部件进行检测,以便及时了解零件的状况,保证装配及维修的精度和质量。
1.7.1 测量误差及量具的选用
计量器具根据其测量使用场合的不同,可分为长度量具、角度量具两大类。常用的长度量具主要有:钢直尺、游标卡尺、高度尺、深度尺、塞尺、半径样板尺、百分表、量块等。角度量具主要有:直角尺、万能角度尺、正弦规等。此外,在装配和调整机械设备水平或垂直位置,测量其工作面的直线度、平面度、垂直度、平行度等几何公差时,还常需选用水平仪、光学平直仪等量仪。
熟悉常用量具、量仪的性能及结构特点,掌握其正确的使用方法,并与运用的检测方法相结合,是装配、维修操作的前提及基础。此外,装配、维修人员还应能根据被测工件尺寸的大小、精度正确选用与之相适应的量具、量仪,而要正确地选用量具进行测量,首先必须对测量误差进行分析。
1.7.1.1 测量的误差
正确的测量,保证测量数值的精准是保证装配质量及精度的重要因素之一,但由于计量器具、测量方法、人员素质等众多原因,造成测量结果不可避免地存在着误差。因此,任何测量结果都不是被测值的真值。但是,通过分析误差的规律、种类和原因,可以采取措施减小测量误差。
(1)测量误差的种类
测量误差按其性质的不同可分为系统误差、随机误差和过失误差三大类。
① 系统误差。在同一条件下对同一个量多次重复测量时,其误差值的正、负号始终保持不变;或者当条件改变时,其误差按一定的规律变化,这类误差称作系统误差。前者称常值性系统误差,后者称变值性系统误差。系统误差可以通过分析和计算得出其数值和符号的正或负,然后对测量结果加入相应的值进行修正,以消除或减小其影响。
② 随机误差。在同一条件下对同一个量多次重复测量时,其误差的大小和符号没有规律,这种误差称为随机误差。随机误差没有规律,无法修正,在足够多的重复测量中,出现正负误差的概率大致相同。因此,可用增加测量次数而取其平均值的方法使其正、负误差相互抵消。这样就可以减小随机误差对测量结果的影响。
③ 过失误差。过失误差,又称反常误差或粗大误差。由于使用了不合格的计量器具、操作错误或读数错误等人为的主观失误,或者由于外界特殊原因(如严重的冲击、振动等)所引起的个别较大误差,称为过失误差或粗大误差。这种误差只能通过把多次测量结果进行分析比较才能发现,而后将其去除。
(2)量具的基本计量参数
计量器具是检测工具中的主要工具,要正确地选用,首先应特别注意其基本计量参数,主要有以下方面。
① 刻度间距。刻度间距是指标尺或刻度盘上两相邻刻线中心的距离。一般刻度间距为1~2.5mm。
② 分度值。分度值又称为读数值,是指标尺或刻度盘上每一刻度间距所代表的量值。常用的分度值有0.1mm、0.05mm、0.02mm、0.01mm、0.002mm和0.001mm等。
③ 示值范围。示值范围是指计量器具标尺或刻度盘所指示的起始值到终止值的范围。
④ 测量范围。测量范围是指计量器具能够测出的被测尺寸的最小值到最大值的范围。如千分尺的测量范围就有0~25mm、25~50mm、50~75mm和75~100mm等多种。
⑤ 示值误差。示值误差指计量器具的指示值与被测尺寸真值之差。示值误差由仪器设计原理误差、分度误差、传动机构的失真等因素产生,可通过对计量器具的校验测得。
⑥ 校正值。校正值又称修正值。为消除示值误差所引起的测量误差,常在测量结果中加上一个与示值误差大小相等、符号相反的量值,这个量值就称为校正值。
(3)减小测量误差的方法
① 减小测量器具本身的误差。应正确选择测量器具的灵敏度、量程范围,并定期校准及正确保养,保持器具有良好的使用状态和技术性能。
② 减小因环境条件引起的测量误差。测量的标准温度是20℃。计量器具的标称尺寸及工件尺寸都是指标准温度下的尺寸。当偏离标准温度较多及工件热胀冷缩性较大时,必须考虑温度的影响。对于高精密度测量,除温度外,还应考虑湿度、气压和振动等因素的影响。
③ 减小测量力及测量方法造成的误差。测量力是指计量器具的测量元件与被测工件表面接触时产生的机械压力。测量力过大会引起被测工件表面和计量器具的有关部分变形,在一定程度上降低测量精度;但测量力过小,也可能降低接触的可靠性。这些均能引起测量误差,应该引起注意,其对高精度的测量影响甚大。因此,必须合理控制测量力的大小,通常情况下测量力的控制范围为(800±200)g。
此外,还应合理选择测量基准和测点。
④ 减小人为主观因素造成的误差。操作人员必须熟悉计量器具的使用方法,认真检查所用器具是否合格,清除被测面的毛刺,操作时精神集中,认真负责,尽量避免操作、读数、计算等方面的失误。
1.7.1.2 常用量具的选用
根据零件的加工精度,合理选用量具,并实施正确的测试方法是保证零件测量数值的正确性及其测量精度的重要因素之一。
(1)零件的加工精度
做到合理地选用量具,必须考虑到零件的精度要求、零件的形状及测量尺寸的大小,以便发挥量具的作用,延长其使用寿命,降低加工成本。零件的加工质量包括多种因素,属于机械加工的因素统称为加工精度。零件的机械加工精度分为四类。
① 尺寸精度。尺寸精度是指零件机加工后的尺寸准确程度,以公差来表示。零件的精度愈高,公差数值愈小。
② 表面形状精度。表面形状精度是指零件机加工后,表面几何形状的准确程度,以形状偏差的大小来表示。形状偏差是机加工后零件的实际形状和理想形状之间的偏差。
③ 相互位置精度。相互位置精度是指零件机加工后各表面之间、表面与轴线之间或轴线与轴线之间相互位置的准确程度,以位置偏差来表示。位置偏差是指零件各表面之间的实际相互位置与理论上的相互位置之间的偏差。
④ 表面粗糙度。表面粗糙度是指零件机加工后表面的粗糙程度。
(2)尺寸的测量量具
对于高度、长度、厚度、深度、外径、内径等简单几何体的尺寸,选用测量量具时,一要考虑测量尺寸的大小,二要考虑测量精度。表1-13、表1-14、表1-15分别给出了游标卡尺、外径千分尺、百分表适用测量精度的范围。
表1-13 游标卡尺的适用范围 单位:mm

表1-14 外径千分尺的适用范围

表1-15 百分表的基本参数 单位:mm

如测量长度尺寸(145±0.035)mm,测量尺寸为145mm,精度要求±0.035mm。可选用200mm×的游标卡尺或测量尺寸为125~150mm的外径百分尺,不仅保证能测尺寸145mm,而且测量精度分别为0.02mm及0.01mm,保证测量准确。
再如测φ40 0+0.027mm的孔,可选用测头尺寸为35~50mm的内径百分表,表1-16给出了常用测量范围内的内径百分表的技术参数。用25~50mm的外径百分尺或量规按尺寸40mm对准内径百分表,将表针调至零位,即可进行测量。这种比较测量法的测量精度为0.01mm。
表1-16 内径百分表的基本参数 单位:mm

若孔的尺寸为φ40 0+0.17mm,因精度低,可直接用精度为0.05mm或0.1mm的游标卡尺进行测量。
(3)角度的测量量具
角度的测量量具常用的有万能角度尺,此外,也可采用水平仪进行测量。
万能角度尺分Ⅰ型万能角度尺[结构见图1-77(a)]和Ⅱ型万能角度尺[结构见图1-77(b)]。

图1-77 万能角度尺的构造
(a)图中:1—直角尺;2—套箍;3—游标尺;4—扇形板;5—主尺;6—基尺;7—直尺
(b)图中:1—圆盘主尺;2—小圆盘副尺;3—游标;4—放大镜;5—锁紧装置;6—微动轮;
7—基尺;8—直尺;9—卡块;10—附加量尺
万能角度尺的技术参数如表1-17所示。
表1-17 万能角度尺的技术参数

(4)表面几何形状的测量量具
零件几何形状的误差,在一般情况下不超过零件的尺寸公差。对于精度高的零件,由于使用性能的需要,几何形状误差要求也严,此时在零件图上应注明。
如某零件图上轴径尺寸注明φ30 0+0.033而没注明其他要求,测量时对轴的椭圆度等几何形状误差,以不超过0.033mm为合格。若图中技术条件要求轴径φ30 0+0.033的椭圆度不大于0.015mm,此时轴的几何形状误差为0.015mm而不是0.033mm。
高精度的零件,其几何形状误差可取尺寸公差的1/3~1/2,对于尺寸公差数值较小的零件,可取其尺寸公差的2/3。
① 直线度的测量量具。直线度是指零件表面直线性误差的程度。不同的测量精度,可采用不同的测量方法,选用不同的量具。常见的测量方法及选用的量具有以下几种。
第一种:塞尺插入法。即利用刀口尺、直尺配合塞尺测量直线度。这种方法适于测量精度要求大于0.02mm的一般长度表面的直线度,测量方法如图1-78所示。

图1-78 直线度的塞尺插入测量法
第二种:透光估测法。透光估测法的测量量具及方法如图1-79所示。主要用于对平面直线度的估测。

图1-79 直线度的透光估测法
第三种:光缝比较法。光缝比较法测量平面的直线度用于对平面直线度要求很高时的测量。测法是将刀口形直尺的刀口放在被测表面上,观察其光缝的大小并与标准光缝进行比较,以判断平面的直线度偏差。
标准光缝是用平板、刀口尺及块规组合而成,如图1-80所示。

图1-80 标准光缝
在刀口尺两端与平板之间放两片尺寸为1mm的块规,中间按需要放不同尺寸的块规,如0.999、0.998、0.997……。将被测表面观察到的光缝和标准光缝比较,从而判断平面直线度的偏差值。
② 平面度的测量量具。平面度是指平面的平整程度,其测量方法和选用的量具 如下。
第一种:刀口尺和直尺测法。用刀口尺和直尺测量平面度,这种方法仅用于精度不高的平面凹、凸的测量。可用直尺或刀口尺测量被测表面不同位置、不同方向的直线度,并借助于塞尺得到误差数值。根据各次测量结果,按几何公差规定做出包容实际表面且距离最小的两平行平面(见图1-81),此两平行平面间的距离Δ即为平面的平面度误差。

图1-81 平面度误差
第二种:平面对研法。用平面对研法检查平面的平面度,这种方法适于检查精度较高的平面。做法是先在被测表面涂上显示剂,再用标准平板与其对研,研后检查在(25×25)mm2面积内的研点数。
若被测平面不是刮研表面,可看其研后接触面积的大小和均匀程度而确定平面度。
用对研法检查平面度时,选用标准平板的面积应大于被测平面的表面。若被测表面的尺寸过大时,也可用水平仪检查。
第三种:平板、百分表测法。用平板、百分表检查平面度(如图1-82所示),首先将被测工件支承于平板上,调整被测平面上的a、c两点等高,b、d两点等高,再用百分表检查整个被测平面,表针显示的最大与最小读数差就是被测表面的平面度。
③ 椭圆度的测量量具。椭圆度误差是指圆柱面(轴或孔)的同一横剖面内最大直径与最小直径之差Δ,如图1-83(a)所示。




测量时可用游标卡尺、外径百分尺测不同方向的轴径,或用卡尺、内径百分表测量不同方向的孔径,再计算出椭圆度Δ=d最大-d最小。
④ 圆度的测量量具。圆度误差是指包容同一横剖面实际轮廓的两个相差最小的圆半径之差Δ,即Δ=R最大-R最小,如图1-83(b)所示。圆度的测量方法有多种,视零件的具体情况而定,常见的测量方法如下。
第一种:对于两端保留顶尖孔的轴,使用两顶尖及百分表测量最为方便。即将轴支承于两顶尖上,百分表放在被测部位,将轴轻轻旋转,表针指示的最大最小读数之差即为轴的圆度误差。
第二种:当轴类零件不准两端保留顶尖孔时,通常用V形铁或标准圆环配合百分表进行测量,分别见图1-84(a)、图1-84(b)。
显然,用V形铁测量时,由于零件转动角度不同,其几何中心高度也有变化,测量误差大,不如用标准圆环测量准确。
第三种:对于孔圆度的测量,可用三点接触式内径百分表进行近似测量,但测得的偏差是直径上的偏差,折半之后才是圆度偏差。

图1-84 圆度的测量
(5)位置精度测量量具
零件各表面相互位置精度有多种情况,测量方法也有所不同,一般采用量具、仪器配合使用进行测量。
① 测量孔轴线与平面的平行度。轴线与平面的平行度,在零件图样上一般给出偏差要求。测时常用平板、心轴、游标高度尺、百分表配合进行,如图1-85所示。
按图示方法测量时,表针的摆差即是两尺寸A、B之差,也就是在指定长度上孔的轴线与平面的平行度。
② 两孔轴线平行度的测量。如图1-86(a)所示,在x—x方向标出两孔轴线的平行度Δx。有两种测量方法。
第一种:当两孔中心距尺寸不大时,可用心轴、游标卡尺或外径百分尺配合进行,量具的精度视被测件的尺寸精度而定。
第二种:当两孔中心距尺寸较大时,按工件的外形,可选用平板、V形铁、心轴、百分表、游标高度尺或滑动表座等配合使用。图1-87所示为连杆两孔轴线平行度的测量实例。




两孔轴线的平行度除x方向外,还有y方向的平行度及测量方法,如图1-86(b)及图1-87所示。
③ 孔系中心距的测量。在箱体或法兰盘类零件的加工或装配中,常遇到孔系的测量,当孔的位置精度较高,孔距尺寸又不大时,可在孔中插入紧配合的标准心轴(如图1-88所示),用外径百分尺量得两心轴的外侧尺寸A,将测得的尺寸A减去两孔的实际半径之和便得到测量中心距。




当孔的位置精度较高,孔距尺寸较大时,常用平板、块规、块规架、游标高度尺、百分表、内径百分表等配合,用坐标方法进行测量,如图1-89所示。
测y—y方向1、2两孔的位置尺寸(150±0.025)mm及(145±0.025)mm的方法是:首先用内径百分表测出孔φ70+00.03mm及φ75+00.03mm的实际尺寸。假设为φ70.02mm、φ75.02mm;然后按图示要求将工件放在平板上,使A面与平板接触;再测孔1的中心尺寸(150±0.025)mm。按尺寸H1=150-35.01=114.99(mm)组成第一组块规,再用装有杠杆百分表的游标高度尺测尺寸H1的上面,并将表针调至零位后,拿开第一组块规,用已对好的高度尺及杠杆表测孔1的最低点,观察表针对零位的偏摆,假如表针多偏摆了一小格,则表示孔的中心比名义尺寸高0.01mm,即实际中心为150.01mm;最后测孔2相对于孔1的中心高l45+00.025mm时,应先将尺寸150.01mm反映在块规架上,可组成一组h1=150.01mm的块规进行块规架调整(如图1-90所示),调好后将块规架锁紧。

图1-89 用坐标法测箱体孔距
1—工件;2—平板;3—杠杆百分表;4—第一组块规;5—第二组块规
按孔2相对于孔1的中心尺寸和孔2的实际半径组成第二组块规h2=
145-37.51=107.49(mm)。将这组块规放在已调好的块规架上,即得到了图1-90所示尺寸H2=h1+h2=150.01+107.49=257.5(mm)。用装有杠杆表的高度尺测
第二组块规的上面(即H2=257.5mm)并将表针调整至零位后,拿开第二组块规及块规架。最后用二次调好的高度尺和杠杆表测孔2的最低点,观察表针的偏摆,若表针多偏摆了1.5小格,则表示孔2相对于孔1的实际中心距为145.015mm。
将工件转90°,使B面与平板接触,用上述方法同样能测量孔1、2在x—x方向的尺寸160+00.025mm及155+00.025mm。
④ 孔间轴线垂直度的测量。图1-91是孔间轴线垂直度的测量实例。




孔间轴线的垂直度,是指在给定长度L上的垂直度。图中是测量箱体1、2两孔在指定长度L上的垂直度。方法是先在1、2两孔内分别插入紧配的心轴,用千斤顶将工件支承在平板上。调整千斤顶,用弯尺将心轴2的位置调成垂直,最后用百分表测量心轴l,百分表在心轴1的长度L内呈现的摆动量,就是1、2两孔在三长度上的实测垂直度。
1.7.1.3 常用量仪的结构及选用
水平仪、光学平直仪等量仪常用于机械设备长而精度高的表面(如导轨面)直线度、工作台面的平面度、零部件间的垂直度和平行度等的测量,在设备的安装和检修时也常用于找正安装位置,在装配操作过程中,其也常常与其他量具配合使用。
(1)水平仪
水平仪按其工作原理的不同,可分为水准式水平仪和电子水平仪两类。生产中应用较多的是水准式水平仪。常用的水准式水平仪有条形水平仪、框式水平仪、合像水平仪三种结构形式,图1-92给出了其结构。

图1-92 水平仪的种类
水平仪是一种以重力方向为基准的精密测角仪器。其主要工作部分是管状水准器,它是一个密封的玻璃管,管内装有精馏乙醚或精馏乙醇,但未注满,形成一个气泡。当水准器处于水平位置时,气泡位于中央;水准器相对于水平面倾斜时,气泡就偏向高的一侧。倾斜程度可以从玻璃管外表面上的刻度读出,经过简单的换算,就可以得到被测表面相对水平面的倾斜度和倾斜角。
① 水平仪的刻线原理。水平仪的刻线原理如图1-93所示。假定平台工作面处于水平位置,在平台上放置一根长度为1000mm的平尺,平尺上水平仪的读数为零(即处于水平状态),若将平尺一端垫高0.02mm,则平尺相对于平台的夹角即倾斜角θ=arcsin(0.02/1000)=4.125″,若水平仪底面长度l为200mm,则水平仪底面两端的高度差H为0.004mm。

图1-93 水平仪的刻线原理
读数值为0.02mm/1000mm的水平仪,当其倾斜4″时,气泡移动一格,弧形玻璃管的弯曲半径R约为103mm,则弧形玻璃管上的每格刻度λ距离为:
即0.02mm/1000mm(4″)的水平仪的水准器刻线间距为2mm。
② 水平仪的读数方法。通常有绝对读数法和相对读数法两种。采用绝对读数法时,气泡在中间位置时,读作“0”,偏离起始端读为“+”,偏向起始端读为“-”,或用箭头表示气泡的偏移方向。采用相对读数法时,将水平仪在起始端测量位置的读数总是读作零,不管气泡是否在中间位置。然后依次移动水平仪垫铁,记下每一次相对于零位的气泡移动方向和格数,其正负值读法也是偏离起始端读为“+”,偏向起始端读为“-”,或用箭头表示气泡的偏移方向。机床精度检验中,通常采用相对读数法。
为避免环境温度影响,不论采用绝对读数法还是相对读数法,都可采用平均值的读数方法,即从气泡两端边缘分别读数,然后取其平均值,这样读数精
度高。
③ 水平仪的应用。三种水平仪中,条形水平仪主要用来检验平面对水平位置的偏差,使用方便,但因受测量范围的限制,不如框式水平仪使用广泛;框式水平仪主要用来检验工件表面在垂直平面内的直线度、工作台面的平面度、零部件间的垂直度和平行度等,在安装和检修设备时也常用于找正安装位置;合像水平仪则用来检验水平位置或垂直位置微小角度偏差的角值。合像水平仪是一种高精度的测角仪器,一般分度值为2″,这一角度相当于在1m长度上其对边高为0.01mm,此时,在相应的水准管的刻线上气泡移动一格,其精度记为0.01mm/1000mm或0.01mm/m。装配机床设备的水平仪分度值一般为4″。
表1-18给出了条形水平仪及框式水平仪的精度等级。
表1-18 条形及框式水平仪的精度等级

④ 水平仪检定与调整。水平仪的下工作面称为基面,当基面处于水平状态时,气泡应在居中位置,此时气泡的实际位置对居中位置的偏移量称为零位误差。由于水准管的任何微小变形,或安装上的任何松动,都会使示值精度产生变化,因而不仅新制的水平仪需要检定示值精度,使用中的水平仪也需作定期检定。
(2)光学平直仪
光学平直仪又称自准直仪、自准直平行光管,其应用与水平仪基本相同,但测量精度较高。外形结构如图1-94(a)所示。

图1-94 光学平直仪
1—目镜;2, 3, 6—分划板;4—聚光镜;5—光源;7, 8—物镜;9—目标反射镜;10—棱镜
图1-94(b)给出了其工作原理。从光源5发出的光线,经聚光镜4照明分划板6上的十字线,由半透明棱镜10折向测量光轴,经物镜7、8成平行光束射出,再经目标反射镜9反射回来,把十字线成像于分划板上。曲鼓轮通过测微螺杆移动,照准刻在可动分划板2上的双刻划线,由目镜1观察,使双刻划线与十字线像重合,然后在鼓轮上读数。测微鼓轮的示值读数每格为1″,测量范围为0′~10′,测量工作距离为0~9m。
1.7.2 测量的方法
测量方法分为直接测量和间接测量两种。直接测量是把被测量与标准量直接进行比较,而得到被测量数值的一种测量方法。如用卡尺测量孔的直径时,可直接读出被测数据,此属于直接测量。间接测量是测出与被测量有函数关系的量,然后再通过计算得出被测尺寸具体数据的一种测量方法。
(1)线性尺寸的测量换算
工件平面线性尺寸换算一般都是用平面几何、三角的关系式进行的。如图1-95(a)所示二孔的孔距L,无法直接测得,只能通过直接测量相关的量A和B后,再通过关系式L=(A+B) /2,求出孔心距L的具体数值。
又如测量图1-95(b)所示三孔间的孔距,利用前述方法可分别测得A、B、C三孔孔距为:AC=55.03mm,AB=46.12mm,BC=39.08mm。BD、AD的尺寸可利用余弦定理求得。
α≈44.38°
那么,BD=AB×sin44.38°=46.12×sin44.38°≈32.26(mm)
AD=AB×cos44.38°=46.12×cos44.38°≈32.96(mm)
图1-95(b)所示BD、AD孔距也可借助高度游标卡尺通过划线测量。

图1-95 孔距的测量
图1-96为圆弧的测量方法。其中,图1-96(a)为利用钢柱及深度游标卡尺测量内圆弧的方法,图1-96(b)为利用游标卡尺测量外圆弧的方法。

图1-96 圆弧的测量
测量内圆弧半径r时,其计算公式为:。若已知钢柱直径d=20mm,
深度游标卡尺读数H=2.3mm,则圆弧工作的半径(mm)。
测量外圆弧半径r时,其计算公式为:。若已知游标卡尺的H=22mm,读数L=122mm,则圆弧工作的半径
(mm)。
(2)角度的测量换算
一般情况下,冲裁件和各类成形工件的角度可以直接采用万能角度尺进行测量,而一些形状复杂的工件,则需在测量后换算某些尺寸。尺寸换算可用三角、几何的关系式进行计算。
图1-97所示零件,由于外形尺寸较小,用万能角度尺难以测量,则可借助高度游标卡尺划线,利用游标卡尺测量工件的尺寸A、B、B1、A1、A2,然后通过正切函数,即求得。

图1-97 角度的测量
(3)常用的测量计算公式
表1-19给出了常用的测量计算公式。
表1-19 常用测量计算公式

