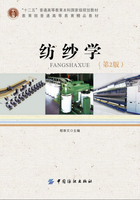
第二节 梳理的基本原理
一、相邻两针面间作用的基本原理
(一)梳理过程中纤维受力
图4-3 作用在针齿上的力
1.力的类型
纤维在梳理机上的运动是其受力的结果,为了研究其运动规律,通过分析,纤维集合体在梳理中的受力情况如图4-3所示。
纤维在梳理中所受的力主要可以分为以下几种。
(1)梳理力R。当两个针面对一束纤维进行梳理时,纤维受到针齿对其的梳理力。梳理力大,则对纤维的梳理、分解效果好,但工艺上也应尽量避免梳理力过大,否则易引起纤维损伤或针布损坏。
(2)离心力C。梳理机上多数工艺部件均作回转运动,转速愈高,纤维受到的离心力愈大。其值可由经典力学公式计算:
C=Mω2r
式中:M——纤维质量;
ω——工作机件转速;
r——工作机件回转半径。
在梳理开始阶段,纤维多为束状,质量较大,离心力较大。离心力虽有使被梳理的纤维及其间的杂质脱离针齿的趋势,但由于纤维间的联系力、纤维与针齿间的摩擦力存在,正常条件下可抵消离心力的作用,纤维不易脱离针齿。而杂质在纤维开松的情况下,很容易被甩掉。
(3)挤压力S。梳理是在两针齿间进行的,而且隔距很小。当纤维层有一定厚度时,纤维间便产生较大的挤压力S,方向指向针根,使纤维进入针隙,增加针齿对纤维的握持力。
(4)弹性反作用力Q。当纤维层受到挤压时,下层纤维会对上层纤维产生弹性反作用力Q,该力方向指向针尖,阻止纤维深入针隙。
(5)空气阻力。在工作件回转时,被其握持的纤维总会受到空气的阻力,其方向与机件运动方向相反,数量级极小,可忽略不计。
(6)摩擦力F。当纤维在隔距很小的两回转针面间受以上诸力作用时,有运动的趋势,此时纤维会受到针齿阻碍其运动的摩擦力F的作用,摩擦力的方向平行于针面。最大静摩擦力的大小直接影响到纤维与针齿的相对运动。
图4-4 沿针运动时力的关系
2.纤维与针齿的相对运动
(1)相对运动类型。纤维受到上述的离心力C、挤压力S、弹性反作用力Q的合力(法向力)U、梳理力R(切向力)及摩擦力F共同作用时,如图4-4所示,纤维相对于针齿的运动有三种情况:
①在针齿间受切向力的作用而被梳理或转移。
②沿针齿向针尖或针根移动。
③纤维在针齿上既不向针齿移动,也不向针间移动,发生所谓的“自制现象”。
在情况①下,纤维作切向运动,且纤维在切向力作用下,实现分梳、转移而形成更小的纤维束,最后形成单纤维,并能使纤维在一定程度上伸直;在情况②下,纤维作沿针运动;在情况③下,纤维可能环绕针齿做相对运动,称纤维的绕针运动。
(2)运动条件。如图4-4所示,切向的梳理力R与法向的合力U(假设U力方向指向针尖时为正值)的合力为T。T与针齿间的夹角β为梳理角,β可能小于90°,也可能大于90°,但恒小于180°。T可分解成为与针齿平行的力Ty及与针齿垂直的力Tx。Ty是使纤维沿针齿移动的力,Tx则是纤维束对针齿的正压力,摩擦力F的大小与Tx有关,它们可用下式表示:
Tx=Tcos(β-90°),Ty=Tsin(β-90°)
纤维若要沿针齿运动,必须克服纤维与针齿间的摩擦力F,即
Ty=Tsin(β-90°)>F=μTcos(β-90°)
tan(β-90°)>μ=tanφ
β>φ+90°
式中:μ——纤维与针齿间的摩擦系数;
φ——摩擦角。
故当β>90°且β>φ+90°时,才会使纤维沿针齿向针尖移动;而当T的梳理角β<90°且β<90°-φ时,才会使纤维沿针齿向针根移动。
同样,按上述方法可求得:
图4-5 纤维在针齿上运动方式的空间区划
当(90°-φ)≤β≤(φ+90°)时,纤维被阻留在针齿上,发生上述第③种情况即“自制现象”。
根据以上分析,可将纤维在针齿上可能的运动方式直观地用图4-5所示的圆锥空间表示。
①当梳理角β>φ+90°时,处于滑脱区,纤维沿针齿向针尖移动。
②当β<90°-φ时,处于沉降区,纤维沿针齿向针根移动。
③当(90°-φ)≤β≤(φ+90°)时,处于自制区,发生“自制现象”,纤维环绕针齿运动。
沿针运动是纤维在针面间转移的基础,绕针运动是梳理的基础,而切向运动则是分梳和转移的实现。
(二)相邻两针面间的基本作用
梳理机上有相互作用的机件基本上都是外层包有针布作回转运动的工艺件。当两针面的距离小到能对纤维起作用的情况下,纤维在两针面间所受到的作用是遵循上面所述的纤维受力及纤维与针齿相对运动分析的规律的,其作用的种类,是由两机件的回转方向、针面相对速度和针齿倾斜方向所决定的。两针面间的基本作用实质上有以下几种。
1.分梳作用
分梳作用见动画4-3,针面产生分梳作用的配置如图4-6所示。由图可见,产生分梳作用时,两针面上的针尖相对,针齿倾斜方向相互平行,两针面间距很小。图4-6(a)中A针面与B针面运动方向相反,所以使处于两针面间的纤维束受到张力,产生梳理力R。R可分为沿针齿作用力P和垂直于针的作用力Q。两分力的大小可以近似表示为:
P=Rcosα
Q=Rsinα
式中:α——工作角,近似等于针齿倾斜角。
力P的方向指向针根,使纤维向针根运动,针齿握持纤维。两针面以逆对针间运动时,A针面握持的纤维尾部被B针面梳理伸直;反之,B针面握持的纤维尾端被A针面梳理伸直。纤维束被A、B针面均握持时,若梳理力大于纤维束强力,则纤维束被一分为二,A、B针面各得一部分纤维,这种作用称为分梳。图4-6(b)、图4-6(c)所示两种情况与图4-6(a)相同,同样可发生分梳作用。因此,产生分梳作用的两针面配置条件如下。
(1)两针面相互平行配置。
(2)任一针面对另一针面的相对运动方向是逆对着针尖的。
(3)两针面的隔距足够小。
或根据力的分析,当两针齿间纤维受到的沿针分力方向均指向针根时,发生分梳作用。
分梳作用的特点是不管两个作用针面中的一个或两个带有纤维,分梳结果必然使两个针面都带有纤维,即原来没有纤维的针面必将抓取部分纤维。因此,可利用分梳作用来实现部分纤维由一个针面向另一个针面的转移。
图4-6 分梳作用
2.剥取作用
剥取作用见动画4-4。两针面配置如图4-7所示时,其间纤维受到力R作用,所产生的沿针分力P,在一个针面上是指向针根的,而在另一针面上则是指向针尖的。因此,纤维能脱离一个针面被另一个针面抓取。
图4-7 剥取作用
图4-7(a)中,A、B两针面运动方向相反,A针面剥取B针面的纤维,这种剥取方式称反向剥取。图4-7(b)中,v2=0,v1>0,同样发生A针面剥取B针面纤维。图4-7(c)中,A、B两针面运动方向相同,当v1>v2时,均发生A针面剥取B针面上的纤维,反之,则B针面剥取A针面的纤维。
因此,两个针面产生剥取作用的配置条件如下。
(1)两针面相互交叉配置。
(2)其中一个针面对另一个针面相对运动的方向是顺着针尖方向的。
(3)两针面的隔距足够小。
3.提升作用
提升作用见动画4-5。两针面配置如图4-8所示,针面对纤维的作用力为R,而力R在两个针面上的沿针分力均指向针尖,这种分力可使纤维从针根隙间提起并处于针尖上。
图4-8 提升作用
图4-8(a)中A、B两针面运动方向相同,只有当v2>v1时,方能发生提升作用。图4-8(b)中,两针面运动方向相反,则不论v1、v2多大,均会发生提升作用。可知,两个针面产生提升作用的配置条件如下。
(1)两针面方向平行配置。
(2)任何一个针面对另一个针面的相对运动方向是顺着针尖方向的。
(3)两针面的隔距足够小。
(三)针布
梳理机上对纤维作用的机件基本上为圆筒(弧)形,其外表均包覆有钢针或锯齿。通过这些针齿的作用,使纤维得到伸直、混和均匀。针布的型号、规格基本是标准化、系列化的,故可根据加工原料和工艺件的作用不同,针对性地进行配套选择。针布主要分为弹性针布和金属针布两大类。
1.弹性针布
弹性针布由钢针与底布组成,一般呈条状,其结构如图4-9(b)所示。
(1)底布。底布由硫化橡胶、棉、毛、麻织物等多层织物用混练胶合而成。
(2)钢针。钢针材料一般为中炭钢丝,针尖经压磨和侧磨后,再进行淬火处理,硬度可达HRC58~62。横截面有圆形、三角形、扁圆形、矩形等多种。钢针被弯成“U”形,按一定角度和分布规律植于底布上。钢针分弯脚、直脚两种。
弹性针布的主要参数如图4-9(a)所示,其中γ为植针角,H为总针高,B为钢针下部高度,A为钢针上部高度,S为侧磨长度。
图4-9 弹性针布
2.金属针布
金属针布为全金属梳理专件,一般由中炭钢丝冲击轧制淬火制成,其外形与锯条相似,具有宽大的基部,能承受较大的力,使用中不变形。齿形根据不同用途而异。如图4-10所示,α为齿面工作角,β为齿背角,γ为齿顶角,T为齿距,a为齿顶长,H为齿总高,h为齿深,c为齿壁宽,b为齿顶厚,d为齿根深,w为基部厚度。
图4-10 金属针布
二、梳理机的针面负荷及分配
(一)针面负荷的意义及种类
针面负荷是指梳理机各辊筒单位面积针面上纤维层的平均重量,其单位为g/m2。各辊筒负荷的大小,实质上反映了纤维层的厚度变化,它不仅与喂入量有关,也与梳理机各项工艺参数及针布规格等有关。合理控制各辊筒的负荷,不仅有利于高产、优质、低消耗,而且能延长针布的寿命。当负荷过小时,不利于纤维的均匀混和;而当负荷过大时,则易梳理不充分,并可能造成对纤维和针布等的损伤。
梳理机的负荷可分为两大类。一类为参与梳理作用的,如喂入负荷αf、返回负荷αb、出机负荷α0,盖板梳理机上还有盖板负荷,罗拉梳理机上还有交工作辊负荷β和剥取负荷β1等。另一类为不参与梳理作用的,如在使用弹性针布的梳理机上,由于针布的梳针高且有弯膝,纤维一经沉入针隙不易上浮,形成的抄针层负荷为αs。
(二)各种负荷的形成及作用
1.盖板梳理机锡林负荷
在盖板梳理机上,锡林上的纤维负荷主要是:喂入负荷αf、盖板负荷αg、盖板花负荷αg1、锡林负荷αc、返回负荷αb、出机负荷α0和抄针层负荷αs,由于现代梳棉机的锡林上均采用金属针布,故其抄针层负荷很小,可以忽略不计。
(1)喂入负荷。是指由喂入罗拉喂入的原料,经刺辊后到达锡林,在锡林上形成的单位面积纤维量,以αf表示,单位为g/m2,一般为0.25~0.4g/m2。
(2)盖板负荷。喂入锡林的喂入负荷与锡林上的返回负荷一起,进入锡林与盖板的梳理工作区,锡林上的纤维被盖板针齿分梳后一部分转移到盖板上,形成盖板负荷,盖板负荷αg为锡林单位面积针面转移给盖板的纤维量。盖板负荷也可以用每块盖板上的纤维总量表示,一般为1~1.6g。盖板花负荷是指盖板走出梳理工作区时,所带出的(相当于锡林每平方米上的)纤维量,以α′g表示,可以忽略。
(3)锡林负荷。锡林走出盖板工作区带至道夫表面的单位面积的纤维量称为锡林负荷,以αc表示,一般为1.5~3.5g/m2。
(4)出机负荷。出机负荷α0即指锡林单位面积针面上转移给道夫的纤维量,在不考虑梳理中的纤维损耗(如盖板花、落杂等)时,出机负荷等于喂入负荷。
(5)返回负荷。返回负荷αb是指锡林针面上的纤维经过道夫而转移给道夫一部分纤维后,仍留在锡林上的单位面积的纤维量,一般为1~3.2g/m2。
盖板梳理机上,锡林上各部分的纤维负荷分布如图4-11所示。
图4-11 盖板梳理机上的锡林针面负荷分布
①Ⅰ区:锡林上的负荷由返回负荷αb组成。
②Ⅱ区:由于喂入负荷的加入,锡林上的负荷为αb+αf。
③Ⅲ区:由于锡林上的部分纤维被盖板转移(抓取),锡林上的负荷为αb+αf-αg。
④Ⅳ区:锡林负荷为αc=αb+αf;考虑盖板花负荷时,αc=αb+αf-α′g。
2.罗拉梳理机锡林负荷及分布
(1)锡林针面负荷。
罗拉梳理机,特别是包有弹性针布的罗拉梳理机,大锡林上各种负荷的形成比较复杂。首先考察运转正常,即罗拉梳理机单位时间内喂入量与输出量相等时大锡林上各种负荷的生成情况。
设原料经运输辊T喂入大锡林C(图4-12)后,依次通过各工作辊W1、W2、W3和W4的工作区时,一部分纤维将分别被各工作辊抓取,形成交工作辊负荷β。同时各剥取辊S1、S2、S3、S4又将工作辊上的纤维剥下后交还锡林,未被最后一只工作辊抓取的锡林表面剩余纤维,经过风轮F和清洁辊f1、f2,由锡林带向道夫D处,又分配给道夫一部分,而仍留在锡林上的部分纤维形成返回负荷αb。这就是锡林与工作辊、道夫间的分配现象。当大锡林带着返回负荷αb再次通过由它与运输辊T组成的工作区时,与新喂入的原料叠合,再进入新一轮的循环。
图4-12 罗拉梳理机上大锡林的负荷分布
①喂入负荷:原料由喂入罗拉进入梳理机后,经若干辊筒达到大锡林上,分布在锡林上每平方米的纤维量称为大锡林的喂入负荷,以αf表示,单位为g/m2。
②交工作辊负荷与剥取负荷:在正常运转时,锡林每平方米针面交给工作辊的纤维量叫做交工作辊负荷,以β表示,单位为g/m2。工作辊上的纤维转移给剥取辊后又交回大锡林每平方米的纤维量称为剥取负荷,其值也等于β。
③返回负荷与出机负荷:返回负荷是大锡林所特有的,形成的原因是锡林与道夫间针面的作用实质上为分梳作用。纤维分配给道夫一部分后,锡林针面上仍留有纤维。这部分纤维分布在大锡林上,其每平方米针面上的纤维量叫做返回负荷,以αb表示,单位为g/m2。而锡林每平方米针面分配给道夫的纤维量则叫作出机负荷,以α0表示,其在数值上与喂入负荷αf相同。
返回负荷αb和出机负荷α0的组成相同,都是由若干次喂入负荷的部分纤维组成的,这是喂入原料在梳理机内的运动方式决定的。由此可见,返回负荷对纤维的混和与出机负荷的均匀有很大影响。
④抄针层负荷:在采用弹性针布的锡林上,由于钢针的倾斜度小于“自制”的下限,在梳理力的作用下,纤维向针根移动,加上针隙深而大,纤维易进入深处,失去了参与梳理的能力,经较长时间的积累,便形成了抄针层负荷αs。因为抄针层占据了一定的针隙,妨碍钢针对纤维的握持和分梳作用,影响输出纤维网的质量,故在运转一定时间后要进行停车抄针,清除抄针层。
(2)锡林针面上负荷分布。
根据以上分析可知,大锡林各部分的负荷组成是不同的。如图4-12所示,将整个锡林分为Ⅰ、Ⅱ、Ⅲ三种类型的若干区域。
①Ⅰ区:在道夫和运输辊T之间,锡林负荷为αb+αs。
②Ⅱ区:在运输辊T与剥取辊S1之间,锡林负荷为αb+αs+αf。
③Ⅲ区:Ⅲ区分Ⅲ1和Ⅲ2区,Ⅲ1区在剥取辊S1和工作辊W1之间,因大锡林从剥取辊S1上得到β(又称交工作辊负荷,由S1从工作辊W1上剥取下),所以此处锡林负荷为αb+αs+αf+β;Ⅲ2区在工作辊W1和下一剥取辊S2之间,因大锡林分配给工作辊W1部分纤维,则此处锡林负荷减少了交工作辊负荷β,为αb+αs+αf。
依此类推,其余各剥取辊与工作辊间的Ⅲ1区域,锡林上的纤维负荷均为αb+αs+αf+β;各工作辊到剥取辊的Ⅲ2区域,锡林上的负荷均为αb+αs+αf。大锡林上的负荷变化情况有以上三种情况。在工作辊与大锡林之间,三种负荷参与梳理,而在道夫与大锡林之间两种负荷参与梳理,这也表明了梳理机上梳理和混和是非常充分的。
(三)分配系数及影响因素
当两针面的配置为分梳作用时,纤维在梳理作用区内,被相互作用的两针面分成两部分的现象称为分配。相关负荷的比例关系一般用分配系数表示,且分配系数主要有两种,一种是工作辊分配系数,表示纤维在工作辊与锡林之间的分配关系;另一种是道夫转移率(即道夫分配系数),表示纤维在道夫与锡林之间的分配关系。
1.工作辊分配系数
在罗拉梳理机上,锡林与工作辊对纤维进行分梳后,锡林每平方米针面交给工作辊针面的纤维量与锡林每平方米针面参与分梳作用的纤维量的比值叫作工作辊分配系数。
(1)预梳锡林工作辊分配系数。
在预梳锡林上没有返回负荷αb,参与梳理作用的只有喂入负荷αf与剥取负荷β两种。故预梳理锡林的工作辊分配系数为K1。
(2)大锡林工作辊分配系数。
在大锡林上,参与梳理作用的负荷,除了αf、β外还有喂入负荷αb,所以大锡林工作辊分配系数K2用下式表示:
事实上,返回负荷αb比喂入负荷αf大得多,且多由单纤维组成易沉于针根,参与梳理和转移的量较小,而喂入负荷的纤维多呈块、束状浮在针尖,易被工作辊针齿抓取,较多地参与梳理分配。为了能较好地反映纤维负荷分配量的波动,工作辊分配系数K2则应以下式表示:
这样在实际应用中预梳锡林和大锡林工作辊分配系数可用同一公式计算。罗拉梳理机上,工作辊的分配系数一般为20%~40%。
(3)影响工作辊分配系数的因素。
分配系数的选择,通常取决于针面的种类、规格及机台的产量和各机件的速比、隔距等条件。
一般情况下,提高分配系数意味着锡林每平方米针面交给工作辊的纤维增多,有利于加强锡林针齿梳理纤维的作用,以及纤维间的混合作用,提高纤维网质量。
工作辊分配系数主要与下列因素有关。
①随着梳理作用的逐渐完善(纤维松散),锡林上各工作辊的分配系数是逐只下降的。
②当锡林负荷较低时,增加喂入负荷,工作辊的分配系数值会增大,但其增量远小于喂入负荷的增量。
③适当增加工作辊表面速度,会提高分配系数。
④适当减少工作辊梳针工作角有利于提高分配系数。
2.道夫转移率及其影响因素
(1)道夫转移率。
锡林向道夫转移的纤维占参与作用的纤维的百分率叫作道夫转移率。无论盖板梳理机或是罗拉梳理机。在锡林与道夫间只有相当于喂入负荷αf及返回负荷αb的纤维量各以不同程度参与梳理,在正常运转时,出机负荷α0与喂入负荷αf基本相等(忽略纤维损耗)。若道夫转移率以γ表示,则:
但在盖板梳理机上,道夫转移率习惯上是以锡林转一转交给道夫的纤维量占锡林带向道夫的纤维量的百分率表示,通常用下列两种方式来表示。
式中:q——锡林转一转交给道夫的纤维量,g;
Q0——锡林盖板自由纤维量(指当机器停止喂给后,从锡林盖板针面中释放并经道夫输出的纤维量),g;
Qc——锡林离开盖板区与道夫作用前的针面负荷(αc)折算成锡林一周针面的纤维量,g。
Q0测定较简单方便,故γ1主要用于金属针布盖板梳理机;而弹性针布因随时间延长,针面负荷增加,自由纤维量减少,使用γ1有一定缺陷,通常采用γ2。
(2)影响道夫转移率的因素。
采取下列措施,都有利于纤维向道夫的转移,适当提高道夫转移率。
①减少道夫针齿的工作角。
②减少道夫与锡林的隔距。
③减少锡林与道夫的速比(道夫速度高,相当于产量提高;锡林速度适当降低,转移率提高)。
④减小锡林直径(同样线速度下,直径小,则转速高,离心力就大,转移率提高)。
道夫转移率高,表明纤维在梳理机中停留时间短,一方面可以减少由于过度梳理而产生的棉结和纤维损伤问题;另一方面也会在一定程度上影响纤维梳理的充分程度,以及纤维间的相互混和、均匀。传统梳棉机的转移率一般为8%~15%,而目前高产梳棉机转移率可高达20%~30%。
三、梳理机的混和、均匀作用
(一)混和、均匀作用的意义
梳理机的混和作用表现为输出产品同喂入原料相比,在其成分和色泽上更为均匀一致;而均匀作用则表现为输出产品的片段重量比喂入时更加均匀一致。这两种作用是同一现象的两个方面,它是通过针面对纤维的储存、释放、凝聚、减薄等方式达到的。这实质上是各梳理辊筒上负荷变化的结果。
1.混和作用
如前所述,纤维在梳理机的锡林与盖板(或工作辊)间的反复梳理和转移,促使在这些机件上的纤维不断变换,从而产生纤维层间乃至单纤维间的细致混和。同时,由于道夫从锡林上转移纤维的随机性,造成纤维在梳理机内停留时间的差异,使同一时间喂入的纤维,分布在不同时间输出的纤维网内,而不同时间喂入的纤维,却凝聚在同时输出的纤维网内,使纤维之间得到混和。
图4-13 纤维在工作辊上分布
在罗拉梳理机上,当锡林上一部分纤维转移到工作辊上时,由于工作辊的表面线速度比锡林的慢,之前分布在锡林较大面积上的纤维,凝聚、转移到工作辊针面上,从而起到混和纤维的作用。而当工作辊上纤维层通过剥取辊的作用返回锡林时,又和锡林带到此处的纤维发生混和,如图4-13所示,当锡林带着纤维进入工作辊的作用区时,锡林上的一部分纤维A被工作辊W1带走,余下的纤维B继续前行并通过工作辊W2,其中一部分纤维C再被工作辊W2带走。当W1上的纤维A经过剥取辊S1返回锡林时,与锡林新带向工作区的纤维实现了混和。影响这种混和作用的因素是工作辊抓取纤维的能力,抓取得越多,则混和作用越好。
2.均匀作用
若将正常运转的梳理机突然停喂,可以发现输出的纤维网并不立即中断,而是逐渐变细。一般使用金属针布梳理时,这种现象可持续几秒钟,而弹性针布则更长些。将变细的条子切断称重,便可得到如图4-14所示的曲线2—7—8。如果在条子变细的过程中恢复喂给,条子也不会立即恢复到正常重量,而是逐渐变重,如图4-14的曲线7—6。可见在机台停止喂给和恢复喂给过程中,条子并不按图4-14中曲线1―2―3—4—5—6那样变化,而是按曲线1—2—7—6变化。这表明在停止喂给时,针齿放出纤维,放出量为闭合曲线2—3—4—7所围的面积。在恢复喂给后,针齿吸收纤维,吸收量为闭合曲线5—7—6所围的面积。这种针齿吸放纤维,缓和喂入量波动对输出量不匀影响的作用,称为梳理机的均匀作用。
图4-14 均匀作用试验
从前面分析可知,当喂入量波动较小,而片段较短时,梳理机有着良好的均匀作用,同时当纤维由锡林向工作辊或道夫转移时,由于锡林表面线速度通常是道夫表面线速度的20~30倍,因而产生20~30倍的并合机会,又使纤维得到进一步的混和、均匀,使输出条的短片段不匀较小。但当喂入纤维量的不匀片段较长,足以引起锡林负荷等发生较大变化时,出条的重量还是会发生波动,梳理机的均匀作用只是使其波动得到缓和。
以上所述及的梳理机的混和、均匀作用,只能在机器的纵向(原料在机内前进的方向)实现,不能在横向实施。若要实现原料的横向混和,必须安装专门的机构(如粗纺梳毛机上的过桥机等)才能达到。
(二)影响混和均匀作用的因素
盖板梳理机的混和、均匀作用的完善程度与锡林与盖板之间的分梳、转移作用及自由纤维量或道夫转移率有关;罗拉梳理机混和、均匀作用则取决于工作辊的分配系数、道夫分配系数。
工作辊分配系数较大,表明有较多的纤维进行反复混和。这有利于加大纤维在机内的储存量,完善混和、均匀作用。道夫分配系数(即道夫转移率)则正好相反,分配系数(转移率)小时,锡林上的返回负荷大,有利于加大纤维在机内的储存量,也有利于改善混和均匀作用。若适当减小工作辊与锡林间的隔距或减小工作辊速比(即锡林表面线速度与工作辊表面线速度之比),则能加大工作辊的分配系数,改善混和均匀作用;若加大道夫与锡林间的隔距,可使锡林的返回负荷增加,以增强混和、均匀作用,但这又与加强分梳有矛盾。因此,在实际生产中必须根据产品要求适当掌握。