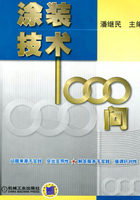
3.6 非铁金属材料涂装前表面预处理
3.6.1 如何进行非铁金属表面脱脂?
同钢铁材料一样,非铁金属制品在加工、贮运过程中粘附的油污,如不除净将严重影响表面处理质量和涂层的附着力。由于非铁金属不像钢铁那样耐强碱腐蚀,发生腐蚀的pH界限值较低,金属腐蚀的pH值界限见表3-52。因而,宜用有机溶剂或表面活性剂法脱脂。若用碱液脱脂,应选用弱碱配方,非铁金属碱液脱脂配方见表3-53。
表3-52 金属腐蚀的pH值界限
表3-53 非铁金属碱液脱脂配方
非铁金属的脱脂方法与钢铁材料类似,可采用碱液法、表面活性剂法和有机溶剂法进行脱脂,其具体内容参照钢铁材料预处理工艺。
3.6.2 如何进行非金属表面化学除锈?
常用的几种非金属表面化学除锈工艺的配方见表3-54。
表3-54 常用的几种非金属表面化学除锈工艺的配方
(续)
① 数字为该酸的密度,单位为g/cm3。
3.6.3 铝及其合金表面预处理包括哪些内容?
铝在空气中会形成致密的氧化膜,具有较好的防锈性能,相对于纯铝,铝合金强度高但防锈性能稍差。且铝及其合金表面光滑,不利于涂层附着。其加工过程中,也会带来油污和灰尘,影响附着力。为了提高它们的耐蚀性,需要进行表面预处理和涂装保护。
脱脂是表面预处理的第一道工序,要注意铝表面不能用强碱清洗,一般采用有机溶剂和表面活性剂方法脱脂。
除去铝及铝合金表面锈蚀等污物时,要尽量不损伤原有完整的氧化膜,所以通常采用细砂纸或研磨膏轻轻打磨表面,必要时,采用竹片除去旧涂膜等污物。应避免使用石墨和含铜、铅等金属材料的底漆,因为这些物质在潮湿条件下会与铝表面发生不良反应,但可使用含锌的底漆,工业生产中最常用的是锌铬黄底漆。对于铝及铝合金表面,通常采用氧化方法进行防锈处理,需注意的是化学转化后表面要在24h内涂上底漆,以免影响涂层的附着力。
3.6.4 镁合金表面预处理包括哪些内容?
镁合金密度小,比强度和比刚度高,是重要的航空材料之一,但镁的化学活性很高,在潮湿和沿海地区很容易遭到腐蚀。镁合金的天然氧化膜薄而不致密,机械强度也不高,极易被破坏而再次腐蚀,而且其氧化产物为碱性,对有机涂层有较强的破坏作用。所以涂装前,必须将天然氧化膜全部除去。镁合金除了表面预处理和涂装保护外,还需增加封闭处理。
(1)油、锈及污物的清除 首先,刷洗表面的非油性污物,然后根据具体情况采用机械除锈、溶剂、碱脱脂、酸中和等方法,可以单一使用或组合使用。
(2)化学转化处理 镁合金的转化,主要采用化学或电化学氧化法,在其表面形成一层薄而均匀的氧化膜,可以大大提高镁合金的防锈能力,提高表面的耐蚀性。
(3)封闭处理 镁合金的化学稳定性较差,尤其是在水汽存在条件下极易腐蚀,所以,在进行了化学转化处理后,还需要封闭处理。即采用耐久、耐水、柔软的树脂进行浸渍,常用的材料是环氧酚醛树脂液,封闭工艺如下:
1)干燥处理,将工件预热到100~110℃,保温10min,以除去微孔中的水分。
2)冷却至60℃±10℃,浸入环氧酚醛树脂液中,通过转动使工件各部分全部粘满树脂液,从树脂液中提出,保持15~30min,至底部不再有多余的树脂液滴下,放入130℃±5℃烘箱烘烤15min。
3)再次冷却至60℃±10℃,再浸入到树脂液中,重复进行封闭操作三次,注意控制封闭膜的厚度,控制在25μm以内。对于大型物体,可以采用喷涂的方式进行封闭操作。
(4)氧化膜的去除 对于镁合金表面不合格的氧化膜,可用化学方法去除。去膜溶液的配方及操作条件见表3-55。
表3-55 镁合金表面处理不合格氧化膜去除溶液的配方及操作条件
3.6.5 镁合金表面脱脂的方法有哪些?
镁合金表面脱脂方法见表3-56。
表3-56 镁合金表面脱脂方法
3.6.6 镁合金表面化学转化处理方法有哪些?
1.化学氧化法
镁合金表面化学氧化法以铬酸盐酸性氧化法最为常用。常用的化学氧化法及其优缺点见表3-57,常用的铬酸盐酸性氧化法的溶液配方及操作条件见表3-58。
表3-57 常用的化学氧化法及其优缺点
表3-58 常用的铬酸盐酸性氧化法的溶液配方及操作条件
① 为质量分数。
对镁合金的锻造件进行化学氧化,其铬酸盐酸性氧化方法的工艺流程为:碱液清洗→冷水洗(去离子水)→铬酸溶液氧化→在NaCr2O7.2H2O 180g/L和HNO3180g/L溶液中于21~32℃浸泡处理0.5~2min→取出后在空气中停留5s→冷水淋洗→重铬酸盐封闭(在NaCr2O7.2H2O 120~180g/L,CaF2或MgF22.74g/L溶液中于99~100℃浸泡30min)→热水淋洗。
若处理镁合金铸造件,只需在第三步(即铬酸氧化溶液)中增加NaHF2、KHF2或NH4F215g/L即可,其余各步骤不变。
2.电化学氧化方法
电化学氧化方法又称阳极氧化方法,其溶液配方及操作条件见表3-59。
表3-59 镁合金电化学氧化方法的溶液配方及操作条件
① 为质量分数。
其工艺流程为:碱液清洗(选择合适的清洗溶液,在88~100℃清洗3~10min)→冷水淋洗→阳极氧化→冷水淋洗。
对于不能应用有机物涂饰或以提高耐蚀性为目的的工件,可增加封闭处理作为其最后一个步骤。
3.6.7 锌及锌合金表面预处理有哪些内容?
锌及其合金在工业上的应用主要是各种镀锌板和锌铝合金,其表面平滑,涂膜附着不牢固。又由于锌合金压铸件疏松多孔,化学稳定性较差,很容易在酸、碱性溶液中腐蚀。铸件表面存在成分偏析现象,在脱脂、活化时,会使某些偏析相优先溶解,表面产生针孔,破坏锌面与涂层的结合力。所以,通常要进行表面预处理(转化),以形成一个防止锌皂形成的保护膜,增大表面粗糙度值,提高涂层附着力。
(1)油、锈及污物的清除 用磨光、抛光等方法,去除表面的非油性污物,然后用非离子型清洗剂水溶液进行脱脂,并彻底洗净,不得残留清洗剂,或用有机溶剂脱脂,但要注意经常更换抹布,以防止重新粘污。随后使用钢丝刷和砂布进行除锈,锈蚀严重时,可采用轻微喷砂处理。
(2)清除旧漆层 根据旧漆层的实际情况采用砂纸打磨,手工工具处理或用化学、加热方法去除旧漆层,也可以选择合适的脱漆剂进行脱漆。
(3)化学转化处理 锌及其合金的转化,主要采用磷化及其后的钝化。磷化膜的主要成分都是单一的磷酸锌,磷化迅速,但会致使二次附着力较低。其钝化膜的质量为1g/m2左右。化学转化后的表面要在24h内涂上底漆,或涂磷化底漆,以免影响附着力。
(4)有机涂层 通常采用锌铬黄作底漆,或使用锌粉底漆、铅酸钙底漆和磷化底漆。避免使用含石墨和铅、铜等金属材料的底漆和油性漆,因为这些物质或其产物在潮湿条件下,会与锌表面发生化学反应,产生针孔,破坏涂层结合力。此外,由于锌及锌合金表面疏松多孔,第一道漆应稍作稀释,一般添加总量10%~20%(质量分数)的稀释剂,以便更好地封闭这些微孔。
3.6.8 锌的钝化处理方法有哪些?
锌及其合金钝化处理的方法很多,按其处理溶液的浓度可分为低浓度、中等浓度和高浓度铬酸盐钝化处理三种。
(1)低浓度铬酸盐钝化处理 这种方法的优点是溶液中含铬量很低,可以节省大量的铬酐,废水中含铬量很少,可以减少废水处理费用,获得的钝化膜的质量与高浓度铬酸盐钝化的质量基本相同。因而实际使用中被广泛应用。其溶液配方及操作条件见表3-60。
表3-60 锌及其合金低浓度钝化溶液配方及操作条件
(2)中等浓度铬酸盐钝化处理 其溶液配方及操作条件见表3-61。
表3-61 锌及其合金中等浓度钝化溶液配方及操作条件
(3)高浓度铬酸盐钝化处理 其溶液配方及操作条件见表3-62。
表3-62 锌及其合金高浓度钝化溶液配方及操作条件
3.6.9 铜及铜合金的表面预处理包括哪些内容?
1.化学氧化
铜及其合金经氧化处理能在表面生成一层薄而致密、与基体结合形成牢固的氧化膜。这种氧化膜在湿度不大的大气中具有良好的稳定性,也是有机涂膜的良好底层,可以提高涂层的耐蚀性。
2.电化学氧化
电化学氧化的溶液组成及操作条件见表3-63。
表3-63 电化学氧化的溶液组成及操作条件
实际操作时,应注意以下事项:
1)重新配制的溶液应当用铜阳极处理至浅绿色,才能进行氧化处理。
2)溶液中氢氧化钠的浓度和氧化温度应控制在规定范围的上限。
3)氧化处理所需的时间应根据电解处理的实际情况来确定。
4)在氧化处理前应先预热2~5min,然后在0.3~0.5A/dm2的电流密度下处理10~20min,再将电流密度调至规定范围的上限,继续处理3~5min后,才能进行氧化处理。
3.氧化膜的去除
经过氧化处理的工件,对于不合格的氧化膜可以使用下列溶液去除:
1)质量分数为10%的硫酸溶液。
2)质量分数为10%的盐酸溶液。
3)铬酐30~90g/L和硫酸15~30g/L的混合溶液。
实际使用时,可以根据实际情况合理选择。
4.钝化处理
铜合金也可以在铬酸或重铬酸盐溶液中钝化处理,形成钝化膜,提高其防护能力。铜及其合金钝化溶液的配方及操作条件见表3-64。
表3-64 铜及其合金钝化溶液的配方及操作条件
对于不合理的钝化膜,可以用下列溶液去除。
1)质量分数为10%的硫酸溶液。
2)质量分数为10%的盐酸溶液。
3)200~400g/L的氢氧化钠溶液。
3.6.10 铜及铜合金化学氧化方法有哪些?
铜及其合金可以在含氧化剂的碱溶液中或铜氨溶液中化学氧化,也可以在碱性溶液中阳极氧化。
1.铜氨溶液处理
铜氨化学氧化溶液的配方和操作条件见表3-65。
表3-65 铜氨化学氧化溶液的配方及操作条件
① 为质量分数。
为了保证铜合金表面的氧化膜质量,铜合金工件氧化前应进行表面预处理。其处理溶液的配方及操作条件见表3-66。
表3-66 黄铜氧化预处理溶液的配方及操作条件
同时,为了提高氧化膜的质量,应注意:①氧化时使用的家具不可使用纯铜制造,应用铝、钢、黄铜制造;②氧化处理的时间应合理控制;③氧化后的工件应清洗干净,并在100~110℃下烘干30min。
2.过硫酸盐碱性溶液氧化处理
过硫酸盐碱性溶液氧化处理的溶液配方和操作条件见表3-67。
为了提高铜合金表面处理氧化膜的质量,应注意以下事项:
1)纯铜工件可以直接在上述溶液中进行氧化处理。而铜合金则应先镀上3~5μm的铜层后再进行处理。
2)氧化处理时,应控制好溶液的组分和浓度。
3)合理控制溶液的温度。
4)在氧化过程中,应不断搅拌。
5)氧化后的工件应清洗干净并烘干处理。
表3-67 过硫酸盐碱性溶液氧化处理的溶液配方及操作条件
3.6.11 怎样定量评定表面可视清洁度?
钢材表面的可视清洁度主要指其表面锈蚀、氧化皮等的清洁状况。其定量评定方法一般有两种:
1)第一种方法是利用氧化皮和铁电阻不同的特点,采用电阻测量仪测定处理后的表面与探头(直径1mm的球形笔状电极)之间的过渡电阻,通过各点的平均值判断表面清洁度。
2)第二种方法为硫酸铜法,其内容是将硫酸铜溶液刷在处理后的钢板表面,除锈完全的部分呈金属铜的颜色,而大于0.5mm残留氧化皮的部分呈暗色,从而判断表面的清洁程度。
还可利用带有蓝色过滤器的光线反射测量仪进行表面清洁度。为了能正确、方便地评定钢材在除锈之后的表面处理质量,我国有相应的国家标准GB/T 8923.1—2011、GB/T 8923.2—2008和GB/T 8923.3—2009。
3.6.12 怎样评定二次除锈表面的可视清洁度?
为了能正确评定二次除锈的质量等级,全国船舶标准化技术委员会发布了标准CB/T 3230—2011《船体二次除锈评定等级》。
该项船舶专业标准将二次除锈前钢材表面状态分为三类(即:W—涂有车间底漆的钢材经焊接作业后,重新锈蚀的表面;F—涂有车间底漆的钢材经火工矫正后,重新锈蚀的表面;R—涂有车间底漆的钢材,因暴露或擦伤而重新锈蚀,或附有白色锌盐的表面),然后根据以不同方式除锈之后钢材表面清洁程度,将二次除锈质量分为若干等级。其质量等级对应关系见表3-68。
表3-68 二次除锈质量等级对应关系
3.6.13 怎样评定钢材的表面粗糙度?
为了定量地描述和比较喷射除锈后钢材表面的粗糙特性,我国制定了GB/T 13288—1991《涂装前钢材表面粗糙度等级的评定(比较样块法)》。
表面粗糙度基准样块由四个具有不同粗糙度的部分组合而成,其值和误差见表3-69。
表3-69 ISO比较样块各部分表面粗糙度
注:1.表中G样块为喷射棱角砂类磨料而获得的表面粗糙特征的样块。
2.S样块为喷射丸类磨料而获得的表面粗糙特征的样块。
3.粗糙度参数Ry是根据ISO 8503—4用触针法测量的粗糙度参数,Ry系指“最大峰-谷”高度。
3.6.14 如何划分表面粗糙度等级?
表面粗糙度等级划分见表3-70。
表3-70 表面粗糙度等级划分
3.6.15 表面粗糙度的评定步骤是什么?
1)清除被测工件表面的浮灰和碎屑。
2)根据所用磨料的类型,选择比较样块G或S的四个部分依次进行对比,必要时可使用放大倍数不大于7倍的放大镜观察。
3)按表3-70所示的定义确定其等级。
除上述方法外,还可直接采用数字式表面轮廓仪、带有探针和千分尺的测量仪或弹簧测微计直接测量,或截取样块后用显微镜直接观察。
3.6.16 怎样进行钢材表面可溶性盐分和灰尘的评定?
钢材表面存在灰尘,对于其涂层的质量有一定的影响;钢铁件经过除锈处理以后,表面还会残存无色的铁盐、氯化物等可溶性盐,这些可溶性盐在腐蚀坑的底部会破坏基体与涂层的结合。为了更好地检测和评定其清洁程度,国际标准ISO8502给出了一系列检测钢材表面可溶性盐和灰尘的评定。
(1)可溶性盐的评定 对经过喷射除锈后的钢材表面残留的可溶性铁盐的检测方法及其评定结果可参照ISO 8502—1-2001标准。对存在于已除过锈的钢材表面上可溶性氯化物的检测方法可参照ISO 8502—2-2005标准。
(2)灰尘的评定 钢材表面灰尘粘污程度的检测方法及其评定标准可参照ISO 8503—3-1992标准。该标准把钢材表面灰尘颗粒大小和灰尘粘污程度分别分为6个等级。