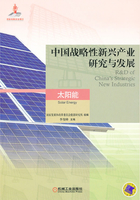
2.2 全球太阳能光伏发电产业发展现状与趋势
2.2.1 多晶硅
1.产业规模
2008年前,全球多晶硅企业主要以传统的七大企业为主(Hemlock、Wack-er、REC、MEMC、德山、三菱、住友),它们占据全球90%以上的市场份额,在2008年之后,韩国OCI公司异军突起,产能急剧增大,2010年已达到2.7万t。2009—2010年,我国多晶硅企业快速发展,其中保利协鑫能源控股有限公司(以下简称保利协鑫)2010年产量已位居世界第三。据估算,2010年全球多晶硅产量达到16万t,主要多晶硅企业产量如图2-16所示。随着多晶硅市场需求不断升温,这些多晶硅企业凭借其技术和资金优势,也在加大布局,纷纷宣称计划扩大产能,预计这些国际大厂的产能将重攀新高。

图2-16 2010年全球部分多晶硅企业产量
2.发展特点
全球多晶硅材料生产呈现出以下几个特点:
1)生产成本较低。国外多家多晶硅企业本身就在化工集团内部或拥有自己的化工厂,化工材料来源丰富、价格低廉。此外,有的企业(如Hemlock、Wacker等)拥有自备电厂,电力成本较低。
2)产业集中度较高。经过多年的发展,由于技术等因素,国外多晶硅企业数量不多,主要集中在传统制造多晶硅的7家企业当中。这些企业规模大,技术水平高,生产成本低,市场占有率高。
3)生产技术水平较高,副产物实现循环利用。上述企业的生产技术水平高,综合能耗较低,副产物循环利用率较高,多数企业真正实现了闭环生产,物料的综合利用率明显比国内多晶硅企业高。
3.发展趋势
1)单位太阳电池硅材料消耗量逐步降低。随着技术的进步,世界单位太阳电池硅材料消耗量正逐年降低,2008年约为8.5t/MW,2010年下降到7.2t/MW,而我国英利绿色能源控股有限公司(以下简称英利)的硅材料消耗已降至5.8t/MW。
2)全球多晶硅供给需求基本趋于平衡。2005年国际多晶硅的短缺导致了国际多晶硅大企业积极扩产,其结果是,在2007年4.2万t产能的基础上,国外主流多晶硅企业在2010年约形成11.4万t生产能力。此外,加上我国生产能力的逐步释放,2011年世界硅料供给趋于缓和并逐步走向平衡。
3)新工艺技术快速发展为调整竞争格局提供了机遇。近年来,在多晶硅生产工艺仍然以改良西门子法占据主要地位的同时,新工艺技术不断涌现。例如,高纯度SiO2直接制取法;熔融析出法;还原或热分解工艺;无氯工艺技术,Al-Si溶体低温制备太阳能级硅;熔盐电解法等。新工艺技术的不断成熟及产业化,将成为未来世界多晶硅产业格局变化的重要推动力。
2.2.2 晶硅电池
1.产业规模
(1)全球晶硅电池片产能、产量2010年,全球晶硅电池片产能保持高速增长势头,已从2009年的16032MW增长到2010年的38699MW,增长141.4%,而产量也从2009年的10500MW增长到2010年的20492MW,增长95.2%,如图2-17所示。

图2-17 2009—2010年全球晶硅电池片产能、产量情况
(2)全球晶硅电池组件产能、产量2010年,晶硅电池组件产能、产量也保持高速增长,组件产能已经从2009年的13636MW增长到2010年的31699MW,增长132.5%,产量从2009年的8128MW增长到2010年的17082MW,增长110.2%,如图2-18所示。

图2-18 2009—2010年全球晶硅电池组件产能、产量情况
2.发展趋势
(1)专业化向垂直一体化的演变 产业的专业化程度是衡量一个产业是否成熟的标志之一。欧美国家对光伏发电技术的研究起步较早,在光伏技术上保持有一定的优势,企业的专业化程度也较高。光伏产业化发展始于2005年,在产业发展的初期,一体化发展易于整合光伏产业链上下游资源,以降低生产成本,提高产品竞争力。另外,光伏产业链较短,为光伏企业的一体化发展创造了良好的条件。我国大多数企业都选择垂直一体化发展,垂直一体化发展的企业电池组件的生产成本也明显低于其他企业。特别是在近几年,全球主要生产光伏产品的国家纷纷下调光伏补贴,推动光伏组件价格下调,以保证光伏系统集成商获取合理的内部收益率。这就需要光伏企业降低电池组件的生产成本,垂直一体化发展成为企业的首选。例如,之前一直专注于电池片生产的德国Q-Cells和我国晶澳在2010年也相继向组件环节发展;我国的尚德也从原先的电池组件向硅片环节发展;日本夏普、美国的Sun-Power、德国的SolarWorld等企业除了继续增强其从硅锭到组件的业务之外,也相继向光伏系统集成方面发展。
(2)产业转移速度加快 光伏产业中下游的电池片/组件工艺日趋成熟,并已逐渐发展成为相对的劳动密集型产业。面对日益增加的组件成本下降诉求,全球晶硅电池组件制造企业加速向资源丰富、要素成本低、市场潜力大的地区转移。美国的SunPower公司2010年在马来西亚开设新的电池制造工厂;德国Q-Cells公司也已在马来西亚建立了电池片制造工厂;日本京瓷公司在我国天津地区建设的工厂已于2010年开工,并且在墨西哥的工厂也于2010年12月投产;而我国台湾地区的光伏企业纷纷将电池组件制造业务往大陆地区转移。
(3)其他行业纷纷涌入 鉴于光伏产业的良好发展前景及大半导体工艺的兼容性,大批传统集成电路及平板显示企业(如台湾积体电路制造股份有限公司(以下简称台积电)、台湾友达、韩国LG和三星等)开始涉足光伏领域。台积电在2010年以62亿台币收购了台湾电池生产厂商茂迪20%的股份,成为其最大的股东,其后又以16.5亿台币入股美国CIGS薄膜电池厂Stion公司,并于2010年年底在台湾建立CIGS薄膜电池工厂。鸿海集团则计划投资20亿元人民币用于太阳电池和组件业务。由于平板显示技术的TFT沉积工序可直接用于薄膜太阳电池的生产,台湾友达、韩国LG和三星等全球最大的几家平板生产厂商,也开始凭借其在平板领域的优势,进入光伏行业。2010年,台湾友达出资3.5亿美元与SunPower公司在马来西亚建厂,并计划投资730亿台币在台湾兴建太阳电池生产基地;韩国LG计划在2015年之前投资8.28亿美元用于发展太阳电池业务;韩国三星计划于2020年前,投资6兆韩元用于发展晶硅和薄膜电池业务。这些传统的半导体厂商资金雄厚,凭借其在半导体制造技术、运营管理及销售渠道等方面的优势,将会对当前的光伏产业格局造成一定的影响。
(4)组件厂商纷纷向系统集成延伸 系统集成的作用,就是按照客户的要求,提供包括产品和技术选择,争取政府政策补贴和项目融资,跟踪维修等全方位的个性化服务,一方面通过打通产业链,促进项目落成;另一方面,通过优化资源配置,降低整体成本。因此,为了更好地控制成本,很多光伏组件企业纷纷向下游的系统集成拓展。我国的苏州阿特斯阳光电力科技有限公司(以下简称阿特斯)将与Unirac公司合作为加拿大的住宅和商业客户安装30MW屋顶太阳能系统,阿特斯将负责项目设计采购施工(EPC)的总承包服务,Unirac公司则提供支架技术。尚德的系统集成团队已经承建了一系列集成太阳能发电系统,包括北京辉煌净雅大酒店120kW幕墙、无锡机场800kW光伏幕墙项目及坐落在无锡的1MW的光伏系统一体化建设的尚德电力总部大楼。同时,利用投资基金GSF(投资全球各地非上市太阳能公司的投资基金)支持各地系统集成项目,拉动下游需求。美国SunPower公司在2010年与南加州爱迪生公司合作,在加州修建并运营3座太阳能电站,总装机容量达到711MW。德国So-larWorld公司于2010年在收购Solarparc AG的过程中也获得了90%的股份转换增加,继续增强SolarWorld公司在系统集成方面的业务。日本Sharp公司于2010年以3.05亿美元收购美国Recurrent Energy公司的股份,继续拓展其在美国的系统集成业务。
2.2.3 硅基薄膜电池
1.产业规模
全球硅基薄膜电池产量随着光伏市场的发展也逐年增加。2005—2010年全球的薄膜电池及硅基薄膜电池产量如图2-19所示。硅基薄膜电池在薄膜电池中的比重呈下降趋势,已从2005年的74.6%下跌到2010年的31%。2010年硅基薄膜电池产量达到850MW,其中日本的硅基薄膜电池产量达到220MW,我国的硅基薄膜电池超过300MW的规模。在2010年,尚德和美国应用材料公司(Ap-plied Materials,AMAT)相继宣布放弃薄膜电池业务转投晶硅电池,日本三洋和夏普也一度推迟了其旗下的硅基薄膜电池生产任务,这给硅基薄膜电池的发展蒙盖了一层阴影。但在2010年下半年,薄膜设备厂欧瑞康宣布其新生产线实现了10%的转换效率和0.5欧元的生产成本,这无疑给硅基薄膜电池注入了一针强心剂。

图2-19 2005—2010年全球薄膜电池和硅基薄膜电池产量
2.产业动态
(1)应用材料暂停薄膜设备业务 美国应用材料公司作为全球最大的非晶硅薄膜设备供应商之一,一度成为业内非晶硅薄膜电池设备技术的顶尖代表。2010年7月,其公布了连续出现营业赤字的能源及环境解决方案部门的重组计划,宣布将停止向新客户销售SunFab系列整套非晶硅薄膜技术及设备,并将业务重点从薄膜技术转向晶硅及发光二极管的制造设备和技术发展上。但是美国应用材料公司还继续向薄膜太阳能制造商销售各种必要工具,包括化学气相沉积和物理气相沉积的设备,也仍将继续推进薄膜电池产品的效率以及气相沉积的产率方面的研发。
(2)尚德放弃薄膜改投晶硅电池生产线 尚德于2010年8月关闭在上海基地建设的硅基薄膜电池,改投晶硅电池生产。在放弃上海薄膜工厂之前,尚德曾于2007年5月宣布投资3亿美元发展薄膜电池,并计划在2010年形成400MW的产能。但此后的国际金融危机让尚德终止了对薄膜电池的投入。2009年,尚德上海薄膜电池工厂的产量只有20MW,而同期尚德的晶硅电池的产量高达704MW。该公司的负责人曾公开表示,薄膜电池与晶硅电池相比,主要是转换效率太低,普遍在7%左右,而无锡尚德的晶硅电池转换效率已经达到了19.12%,为国际领先水平。
(3)三洋推迟薄膜电池生产日本三洋公司于2010年8月宣布暂缓该公司生产薄膜太阳电池的计划,而将精力集中在其原有晶硅电池产品的效率提高和市场占有率上。据该公司披露的信息显示:自从三洋太阳能公司由三洋电器和日本石油公司在2009年1月联合成立以来,光伏市场发生了较大的变化。晶硅电池由于原材料成本降低而成品价格直线下降,大大削弱了薄膜电池的竞争优势。因此,三洋和日本石油公司得出结论,三洋太阳能应该暂缓其母公司的生产扩张计划而将重点转移到提高公司市场竞争力上去。
2.2.4 CIGS薄膜电池
1.产业规模
虽然CIGS薄膜电池的实验室效率是目前产业化的几种薄膜电池中最高的,但由于其生产工艺较难控制,其产业化进展较为缓慢,目前投入规模化生产的仅有德国、美国和日本等国家的一些企业,产能也较低。图2-20所示为2007—2009年全球CIGS薄膜电池的产量情况。

图2-20 2007—2009年全球CIGS薄膜电池产量
2.产业动态
(1)柔性CIGS组件通过UL认证 柔性太阳能光伏技术在2010年获得了UL认证。SoloPower公司的柔性CIGS组件获得了美国保险商实验室(Underwriter Laboratories Inc,UL)的认证,这是薄膜行业首次取得这样的成果。这也是首批进入欧洲和北美市场的大功率柔性组件中获得UL认证的产品。UL1703标准认证是一项衡量光伏组件安全生产的标准,柔性薄膜组件将在一处独立实验室中接受UL1703标准测试,产品在经历一系列严苛的测试之后才会被授予UL认证。SoloPower还表示其进行过大量的内部测试,在安全性、质量和可靠性方面都比UL测试的标准更加严格。
(2)转换效率取得突破 德国太阳能和氢能研究中心(ZSW)使用共蒸镀(co-evaporation)技术制造的CIGS电池,实验室的光电转换效率达到20.3%。此次创造纪录的CIGS太阳电池面积为0.5cm2,厚度为4μm。这项新纪录将CIGS与多晶硅太阳电池的实验室效率差距缩小到只有0.1%。但该实验室负责人表示高效率CIGS薄膜电池的商业化生产还要有一段时间。ZSW预计在未来几年普通CIGS电池的效率将从目前的11%提高到15%左右。目前ZSW正与WürthSolar公司合作开发CIGS电池技术。同时,NREL在一项独立进行的测试中也证实美国MiaSolé公司生产的CIGS薄膜电池(尺寸为1m2)效率达到了15.7%。在产业方面,德国Solibro公司(已被汉能收购)在2012年年底CIGS薄膜产品量产转换效率已达14.7%。
(3)主要厂商纷纷涉足CIGS电池领域 台积电通过收购美国Stion的部分股权,与Stion结成策略联盟,由Stion提供技术,台积电负责生产,目标是成为全球产能前五的PV厂。台积电认为,CIGS因低成本等优势,成长率将最高,到2015年的年复合成长率将达115%。台湾升阳兴股份有限公司则是通过转投资的新能光电科技有限公司,引进德国制造商Centrotherm的设备,目前已引进第一条35MW生产线。德国Q-Cells公司自2009年全部收购CIGS厂商Solibro公司后,于2010年6月11日宣布,大规模生产的CIGS薄膜模块光电转换效率达到13.05%的纪录。该纪录也得到德国弗朗霍夫(Fraunhofer)研究院的确认。
(4)企业纷纷扩产 在2010年全球光伏市场的带动下,各主要CIGS厂商纷纷扩产。美国SoloPower公司在2010年年初宣布将在俄勒冈州威尔逊维尔(Wilsonville)建设一座75MW生产基地,这座CIGS柔性组件工厂完工后将配有4条生产线,总产能将达到300MW,该计划总耗资约3.4亿美元。日本Showa(昭和壳牌)目前已拥有2座年产能分别为20MW和60MW的CIS太阳电池厂,并于2009年9月在日本宫崎县兴建年产能达900MW的太阳电池新工厂(国富工厂)。
2.2.5 碲化镉薄膜电池
1.生产规模
美国First Solar公司主要生产碲化镉薄膜电池组件,自2002年涉足光伏模块业务以来,其制造能力一直稳步上升。2005年,公司年产率达到25MW。之后几年,公司继续扩大规模,至2010年电池组件产能达到1.5GW,产量达到1.41GW,位居全球太阳电池组件产量次席。该公司2007—2010年电池产量如图2-21所示。

图2-21 FirstSolar公司2007—2010年电池产量情况
2010年,First Solar公司投入生产的生产线有24条,分别是马来西亚16条、德国4条和美国4条。而新增的生产线(马来西亚的8条、德国的4条和法国的2条)正在抓紧建设,2010年又宣布在越南和美国新建两处生产基地,这两座工厂各拥有4条生产线。届时,该公司产能将在目前24条生产线的基础上扩大几乎一倍,达到46条。同时,每条生产线的产能也在持续增大,在2010年第三季度,每条生产线的产能已达到59.6MW。届时,该公司产能将达到2742MW。First Solar公司的产能扩张情况如图2-22所示(据First Solar公司最新的财报显示,目前每条生产线的产能达到62.6MW)。

图2-22 FirstSolar公司产能扩张情况
2.生产成本
受益于技术的不断进步,First Solar公司的生产成本逐年下降。在2008年第四季度,该公司的成本已经跌破1美元/W,降至98美分/W,而在2009年再次下跌14%,降至84美分/W。在2010年第三季度,其生产成本已经降至76美分/W,在第四季度,又降至75美分/W。从图2-23所示的数据可以看出,其生产成本的变化近乎直线下降,每个季度平均下降2.5美分。据FirstSolar公司在2011年公布的最新路线图(roadmap)表明,到2014年,预计每瓦的生产成本将降至52~63美分。

图2-23 FirstSolar公司碲化镉电池转换效率和生产成本发展情况