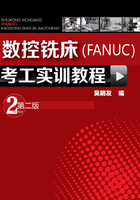
2.6 零件的测量
一般情况下,数控机床加工后工件尺寸的测量方法与普通机床加工后的测量方法几乎相同。测量零件上的某一个尺寸,可选择不同的测量器具。为了保证被测零件的质量,提高测量精度,应综合考虑测量器具的技术指标和经济指标,具体有如下两点。
① 按被测工件的外形、部位、尺寸的大小及被测参数特性来选择测量器具,使选择的测量器具的测量范围满足被测工件的要求。
② 按被测工件的公差来选择测量器具。考虑到测量器具的误差将会带到工件的测量结果中,因此,选择测量器具所允许的极限误差约占被测工件公差的1/10~1/3,其中对低精度的工件采用1/10,对高精度的工件采用1/3甚至1/2。
2.6.1 轴径的测量
轴径的实际尺寸通常用计量器具(如卡尺、千分尺)进行测量。下面简要介绍游标卡尺的结构原理和用法。
① 游标卡尺的结构与工作原理。游标卡尺是利用游标原理对两测量面相对移动分隔的距离进行读数的测量器具。游标卡尺(简称卡尺)与千分尺、百分表都是最常用的长度测量器具。游标卡尺的结构如图2-43所示。游标卡尺的主体是一个刻有刻度的尺身,沿着尺身滑动的尺框上装有游标。

图2-43 游标卡尺
1—尺身;2—内量爪;3—尺框;4—紧固螺钉;5—深度尺;6—游标;7—外量爪
游标卡尺可以测量工件的内尺寸、外尺寸(如长度、宽度、厚度、内径和外径)、孔距、高度和深度等。优点是使用方便、用途广泛、测量范围大、结构简单和价格低廉等。
② 游标卡尺的读数原理和读数方法。游标卡尺的读数值有3种:0.1mm、0.05mm、0.02mm,其中0.02mm的卡尺应用最普遍。下面介绍0.02mm游标卡尺的读数原理和读数方法。游标有50格刻线,与主尺49格刻线宽度相同,游标的每格宽度为49/50=0.98mm,则游标读数值是1.00-0.98=0.02mm,因此0.02mm为该游标卡尺的读数值,如图2-44所示。
mm

图2-44 读数实例
游标卡尺读数的三个步骤如下。
a.先读整数。看游标零线的左边,尺身上最靠近的一条刻线的数值,读出被测尺寸的整数部分。
b.再读小数。看游标零线的右边,数出游标第几条刻线与尺身刻线对齐,读出被测尺寸的小数部分(即游标读数值乘其对齐刻线的顺序数)。
c.得出被测尺寸。把上面两次读数的整数部分和小数部分相加,就是卡尺的所测尺寸。从图2-44示例中可以读出测量值,读数的整数部分是133mm,游标的第11条线(不计0刻线)与尺身刻线对齐,所以读数的小数部分是0.02×11=0.22mm,被测工件尺寸为133+0.22=133.22mm。
游标卡尺使用前要进行检验,若卡尺出现问题,势必会影响测量结果,甚至造成整批工件的报废。首先要检查外观,要保证无锈蚀、无伤痕和无毛刺,而且要保证清洁。然后检查零线是否对齐,将卡尺的两个量爪合拢,看是否有漏光现象。如果贴合不严,需进行修理。若贴合严密,再检查零位,看游标零位是否与尺身零线对齐,游标的尾刻线是否与尺身的相应刻线对齐。另外,检查游标在主尺上滑动是否平稳、灵活,不要太紧或太松。读数时,要看准游标的哪条刻线与尺身刻线正好对齐。如果游标上没有一条刻线与尺身刻线完全对齐时,可找出对得比较齐的那条刻线作为游标的读数。测量时,要平着拿卡尺,朝着光亮的方向,使量爪轻轻接触零件表面。量爪位置要摆正,视线要垂直于所读的刻线,防止读数误差。
2.6.2 孔径的测量
孔的实际尺寸通常用通用量仪(如内径百分表)测量,孔的实际尺寸和形状误差的综合结果可用光滑极限量规检验,适合于大批量生产。在深孔或精密测量的场合则常用内径百分表或测长仪测量。下面简要介绍内径百分表的结构原理和用法。
① 内径百分表的结构。内径百分表的结构如图2-45所示,可换测头2根据被测孔选择(仪器配备有一套不同尺寸的可换测头),用螺纹旋入套筒内并借用螺母固定在需要位置。活动测头1装在套筒另一端导孔内。活动测头的移动使杠杆8绕其固定轴转动,推动传动杆5传至百分表7的测杆,使百分表指针偏转显示工件偏差值。活动测头两侧的定位护桥9起找正直径位置的作用。装上测头后,即与定位护桥连成一个整体,测量时护桥在弹簧10的作用下,对称地压靠在被测孔壁上,以保证测头轴线处于被测孔的直径位置上。

图2-45 内径百分表的结构
1—活动测头;2—可换测头;3—量脚;4—手把;5—传动杆;6—隔热手柄;7—百分表;8—杠杆;9—定位护桥;10—弹簧
② 百分表的工作原理。百分表结构如图2-46所示。在测量过程中,测头9的微小移动,经过百分表内的一套传动机构而转变成主指针6的转动,可在表盘3上读出被测数值。测头9拧在量杆8的下端,量杆移动1mm时,主指针6在表盘3上正好转一圈。由于表盘上均匀刻有100个格,因此表盘的每一小格表示1/100mm,即0.01mm,这就是百分表的分度值。主指针6转动一圈的同时,在转数指示盘4上的转数指针5转动1格(共有10个等分格),所以转数指示盘4的分度值是1mm。旋转表圈2时,表盘3也随着一起转动,可使主指针6对准表盘上的任何一条刻线。量杆8的上端有个挡帽10,对量杆向下移动起限位作用;也可以用它把量杆提起来。

图2-46 百分表
1—表体;2—表圈;3—表盘;4—转数指示盘;5—转数指针;6—主指针;7—轴套;8—量杆;9—测头;10—挡帽;11—耳环
③ 仪器的使用方法。
a.表的安装。在测量前先将百分表安到表架上,使百分表测量杆压下,指针转1~2圈,这时百分表的测量杆与传动杆接触,经杠杆向下顶压活动测量头。
b.选测头。根据被测孔径基本尺寸的大小,选择合适的可换固定测头安装到表架上。
c.调零。利用标准量具(标准环、量块等)调整内径百分表的零点。方法是手拿着隔热手柄,将内径百分表的两测头放入等于被测孔径基本尺寸的标准量具中,观察百分表指针的左右摆动情况,可在垂直和水平两个方向上摆动内径百分表找最小值,反复摆动几次,并相应地转动表盘,将百分表刻度盘零点调至此最小值位置。
d.测量。将调整好的内径百分表测量头倾斜地插入被测孔中,沿被测孔的轴线方向测几个截面,每个截面都要在相互垂直的两个部位各测一次。测量时轻轻摆动表架,找百分表示值变化的最小值,此点的示值为被测孔直径的实际偏差(注意正、负值),如图2-47所示,根据测量结果和被测孔的公差要求,判断被测孔是否合格。

图2-47 内径百分表测孔径
e.复零。测量完毕后应对内径百分表的零点进行复查,如果误差大,要重新调零和测量。
2.6.3 角度的测量
角度是一个重要的几何参数,就具体的零件而言,它包括矩形零件的直角,锥体的锥角,零部件的定位角、转角以及分度角等。常用的测量工具有角度量块、直角尺、多面棱体和万能工具显微镜。下面简要介绍万能工具显微镜的结构原理和用法。万能工具显微镜是机械制造中使用较为广泛的光学测量仪器,它具有较高的测量精度,可用于长度、角度、复杂轮廓形状零件的精密测量。该仪器有多种可选附件,可用直角坐标系或极坐标系测量,主要测量轴径、孔径、锥度、样板、圆弧半径、凸轮坐标尺寸、空间距、模具、刃具、量具、螺纹和齿轮等。
① 仪器的结构形式。仪器的结构见图2-48。

图2-48 万能工具显微镜
1—X方向读数器;2—Y方向读数器;3—归零手轮;4—瞄准显微镜;5—双向目镜;6—立柱;7—反射照明器;8—手轮(调焦距);9—手轮(调立臂倾斜角度);10—Y方向滑台;11—顶尖;12—底角螺钉(3个,调仪器水平);13—制动手柄(向左松开,推、拉手柄,Y方向滑台前、后移动);14—Y方向滑台微动手轮;15—玻璃工作台固定螺钉(2个);16—玻璃工作台;17—底座;18—光栅调整装置;19—X方向滑台制动手轮;20—X方向滑台微动装置;21—X方向滑台;22—X方向滑台分划尺;23—读数鼓轮
② 测量方法。根据被测件的特征,选用适当的附件安装在仪器上;接通电源;调节照明灯的位置;选择并调节可变光栏;工件经擦拭后安装在仪器上;调焦距。角度测量法测量如图2-49所示的V形架的角度α。使用附件有玻璃工作台、物镜和测角目镜。

图2-49 测量实例
a.将工件置于工作台中间。
b.移动X、Y方向滑台,使米字线交点落在被测件的Ⅰ边上,然后移动米字线使中间线与工件的Ⅰ边对准,从测角目镜中读出角度值。再以同样方法将米字线的同一根刻线与工件的Ⅱ边对准并读数。
c.两次读数差为角度α测量值。
2.6.4 表面粗糙度的测量
表面粗糙度的测量方法主要有比较法、光切法、光波干涉法和针触法等。下面简要介绍接触式表面粗糙度测量仪的结构原理和用法。接触式表面粗糙度测量仪利用触针直接在被测件表面上轻轻划过,从而测出表面粗糙度评定参数Ra值,也可通过记录器自动描绘轮廓图形进行数据处理,得到微观不平度十点高度Rz值。
① 表面粗糙度测量仪的结构形式见图2-50。

图2-50 表面粗糙度测量仪
1—底座;2—V形架;3—被测工件;4—触针;5—传感器;6—固定螺钉;7—启动手柄;8—升降手轮;9—立柱;10—驱动箱;11—变速手柄;12—电气箱;13—测量范围旋钮;14—指示表;15—指零表;16—取样长度旋钮;17—电源开关;18—指示灯;19—测量方式开关;20—调零旋钮;21—记录器;22—记录器开关;23—线纹调整旋钮;24—锁盖旋钮;25—记录器变速手轮
② 表面粗糙度测量仪的测量方法。
a.安装。将驱动箱10装在立柱9上的横臂燕尾导轨上,转动升降手轮8,驱动箱可自如升降。将传感器5安装在驱动箱上并用固定螺钉6固定。接好各接插件,然后接电源。
b.读表。将电气箱12上的测量方式开关19拨向“读表”的位置,然后将驱动箱上的变速手柄11转至“Ⅱ”的位置,打开电源开关17,指示灯18亮。粗略估计工件表面粗糙度数值,用取样长度旋钮16选择适当的取样长度,并将驱动箱上启动手柄7轻轻转向左端。升降驱动箱10,使传感器上触针4与工件表面接触,直至指零表15的指针处于两条红带之间。启动手柄7,驱动箱拖动传感器5相对被测件表面移动,指示表14的指针开始摆动,然后停在某一位置上,记下测量结果。将启动手柄7退回原处,准备下一次测量。
c.记录。将测量方式开关19拨至“记录”位置,驱动箱变速手柄11处于“Ⅰ”位置,行程长度选40mm。粗略估计工件表面粗糙度数值,调整记录器变速手轮25,选择适当的水平放大比。升降驱动箱10,使触针4与工件被测表面接触,直至记录器笔尖大致地处于记录纸中间位置,然后打开记录器开关22,启动手柄7轻轻转向右端,开始测量。当需停止记录时,可立即脱开记录器开关22,若在测量的过程中需要传感器停止工作,将启动手柄7拨向左端即可。
2.6.5 复杂三维形状工件的测量
三坐标测量仪是一种高效精密测量仪器,可对复杂三维形状的工件进行快速测量,它是由测头测得被测工件X、Y、Z三个坐标值来确定被测点的空间位置的,其测量结果可绘制出图形或打印输出。
三坐标测量仪综合应用了电子技术、计算机技术、精密测量技术和激光干涉技术等先进技术,主要包括测量系统、控制系统、坐标显示系统和数据输出系统等。三坐标测量仪的基本结构主要包括机床部分(包括工作台、底座、立柱和支架等)、传感器部分和数据处理系统三大部分,见图2-51。三坐标测量仪的工作原理主要是通过测头(传感器)接触或不接触工件表面,由计算机进行数据采集,通过运算并与预先存储的理论数据相比较,然后输出测量结果。适用于各种复杂型面的模具、机械零件、箱体、曲面、工夹具等的几何形状尺寸的直角坐标系或极坐标系的孔距、角度、锥度、直线尺寸、形位公差、径向和轴向振摆等机械尺寸的测量。

图2-51 三坐标测量仪
1—支架;2—工作台;3—测头;4—控制柜;5—打印机;6—数据处理计算机